Go downtown in any major city and take a look around. Most of the buildings towering over you have one thing in common: they're built using just a handful of popular construction types. The structure you choose isn’t just about keeping the roof up—it impacts cost, speed, safety, and even how the building is used day to day.
Steel frame and reinforced concrete are the main players in commercial construction. Ever noticed those massive cranes stacking steel beams like giant Lego blocks? That's steel frame in action—fast, flexible, and able to go tall without breaking the bank. Concrete, on the other hand, gives strength you can count on—schools, hospitals, and banks lean on it for a reason.
- Why Structure Types Matter in Commercial Construction
- Steel Frame Construction: The Heavyweight Choice
- Concrete Structures: Strength and Versatility
- Other Common Methods: Wood, Masonry, and More
- Choosing the Right Construction for Your Project
Why Structure Types Matter in Commercial Construction
Picking the right structure for a commercial building is a big deal—far more important than just ticking a box on a checklist. It decides how tall you can build, how wide your spaces are, and even how the building deals with weather, fire, or earthquakes. For example, steel frames can go higher and create those wide-open office floors you see in modern towers, while concrete structures are champs when you want something solid that resists fire and doesn't sway in the wind.
Here’s the kicker: costs can swing wildly depending on the structure type. Steel frame buildings can often go up faster because a lot of the parts are made off-site. Concrete takes more labor and time but can be cheaper over the long haul because of less maintenance. In some parts of the U.S., you’ll find that concrete or masonry is almost a given because of local building codes, soil conditions, and climate concerns.
There’s also the issue of safety. Most states set strict rules for commercial construction—especially for places like schools or hospitals—because some structures just do better against fire, floods, or even earthquakes. In California, for example, you’ll almost always see reinforced concrete or steel frame because those types hold up best when the ground shakes.
Here’s a quick look at how structure types impact the basics:
Structure Type | Speed of Build | Durability | Common Uses |
---|---|---|---|
Steel Frame | Fast | High | Offices, Retail, High-Rises |
Concrete Structure | Moderate | Very High | Hospitals, Banks, Schools |
Masonry/Wood | Slow | Medium | Smaller Shops, Warehouses |
Bottom line: the type of structure isn’t just a technical detail—it shapes your building’s future, its budget, and even the kinds of businesses that will want to set up shop inside.
Steel Frame Construction: The Heavyweight Choice
If you ask folks in the commercial construction business what dominates the skyline, most will point right at steel frame construction. These structures go up fast and can stack up to dizzying heights. That’s why you’ll find steel frames under almost every modern office tower, big-box retail store, and fancy hotel.
Why is steel such a go-to? First, it's incredibly strong for its weight. You can use less material to get the same or even more strength compared to concrete or wood. That adds up—literally—because less weight means foundations don’t have to be beefed up as much, which cuts costs. Plus, steel frames are pre-engineered and fabricated off-site, so when the beams show up, it’s basically like piecing together a giant, very expensive, adult-sized Erector Set.
Here are a few reasons why steel frame is so popular in commercial buildings:
- Speed: Since most of the work is done in factories, crews can throw up the frame in record time once materials are delivered.
- Flexibility: Want open, column-free spaces for retail or huge conference halls? Steel makes that easy.
- Durability: It laughs in the face of termites, rot, and even fire when properly treated.
- Height: Nothing beats steel when you want to go tall. It’s basically built for skyscrapers.
Of course, steel has downsides. It can get pricey if global steel prices spike, and it needs protection from corrosion, especially in places with brutal weather. But overall, the perks outweigh the pain for most big commercial construction projects.
Quick Stats | Steel Frame Buildings |
---|---|
Average Assembly Speed | Up to 50% faster than concrete |
Max Practical Height | 100+ stories |
Market Share (U.S. High-rise) | Over 80% |
If you’re eyeing a project that needs serious flexibility, speed, and strength, steel frame construction is almost always your best bet—just ask any city skyline.
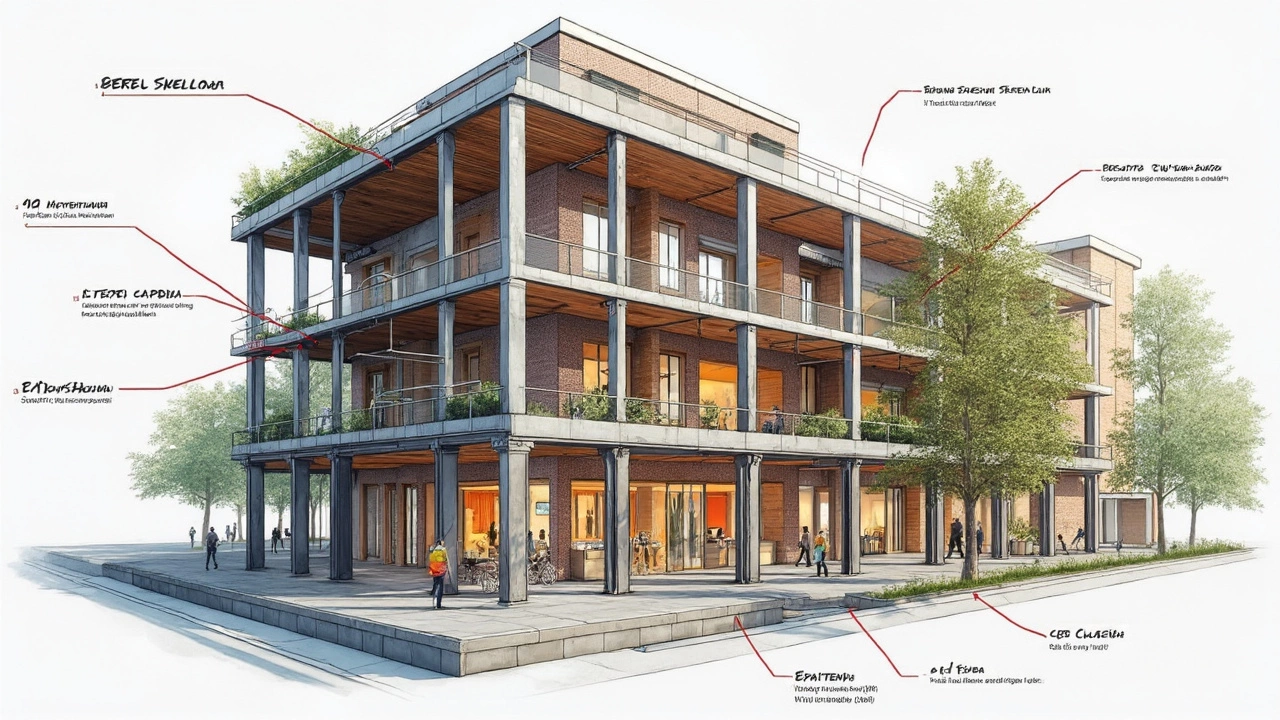
Concrete Structures: Strength and Versatility
When it comes to commercial buildings, you can't beat concrete for all-around toughness and flexibility. Concrete structures show up everywhere—think offices, malls, warehouses, and especially hospitals and schools. Why? This material handles heavy loads and stands up to fire, wind, and everyday wear without flinching.
One big draw is concrete’s versatility. Builders use it for columns, floors, walls, and even entire frames. With modern techniques like post-tensioned slabs and pre-cast panels, you can shape concrete into just about anything. Ever been in a building with massive, pillar-free open spaces? That’s usually thanks to concrete’s power to hold up roofs and upper floors with fewer supports.
Concrete is also a favorite for cost-conscious projects—especially for buildings that don’t need to go super tall. It acts as both structure and fire barrier, which can save money on extra fireproofing. Developers love that it soaks up sound too, making it a hit for hotels, theaters, and office complexes that need peace and quiet inside.
Let’s look at some numbers that show off concrete’s strengths:
Type of Concrete | Typical Compressive Strength (psi) |
---|---|
Standard Ready-Mix | 3,000–4,000 |
High-Strength Concrete | 6,000–10,000+ |
Ultra-High-Performance | 17,000–20,000+ |
Those high numbers make it clear why concrete structures are everywhere in commercial construction. If you’re thinking about using concrete for a project, here are a few key perks:
- Excellent fire resistance without any extra treatments
- Great sound insulation for busy or noisy locations
- Low ongoing maintenance compared to wood structures
- Good value for single-story or mid-rise buildings
On the flip side, concrete takes longer to cure and needs some skill to pour and finish right—so your build might take a little longer than if you were going full steel. Still, all things considered, concrete is a rock-solid choice for most commercial construction projects.
Other Common Methods: Wood, Masonry, and More
Steel and concrete might get the spotlight, but they aren’t the whole story in commercial building construction. You’ll see plenty of smaller or specialized places using wood, masonry, or even hybrids with metal and concrete. Each approach has its niche, especially for certain sizes or types of projects.
Wood framing isn’t just for houses. You’ll find it in low-rise offices, small retail shops, cafes, and medical clinics. In the U.S., codes usually cap wood commercial buildings at four stories, though there are a few exceptions. It’s faster and often cheaper than steel or concrete—plus, it makes it easy to remodel later. But, let’s be real, wood isn’t great for fire resistance and can get chewed up by termites, especially in humid spots.
Next up: masonry. Brick, concrete block, or stone masonry pops up a lot in schools, mid-rise apartments, historic districts, and warehouses. What makes masonry appealing? It’s tough, fire-resistant, and stands up to bad weather. But it’s heavy—think labor-intensive, longer build times, and more structural support needed at the base compared to steel frames. If an insurance company had a say, they'd vote for masonry thanks to its fire-stopping abilities.
Check out these common commercial building types and their preferred construction material:
Building Type | Main Material |
---|---|
Retail strip mall (1-2 stories) | Wood or masonry |
Warehouse | Masonry |
Small medical clinic | Wood or steel |
Historic renovation | Original masonry, plus steel upgrades |
There’s also a move toward hybrid systems—mixing steel, concrete, wood, and even newer materials to get the benefits of each. Modern engineered wood, like cross-laminated timber (CLT), is starting to pop up in offices and mid-rises. It’s lighter than concrete but still strong enough for commercial use, and it looks pretty cool.
"What used to be all about brick-and-mortar is quickly shifting to smart blends—wood adds warmth, concrete gives strength, and steel brings flexibility," says Paul Tebbe, senior architect at Gensler.
If you’re thinking small, want a unique vibe, or need something quick, consider these lesser-known choices. Just make sure to check local codes—some cities have tight rules about what you can use for commercial buildings, especially when it comes to fire and earthquake safety.
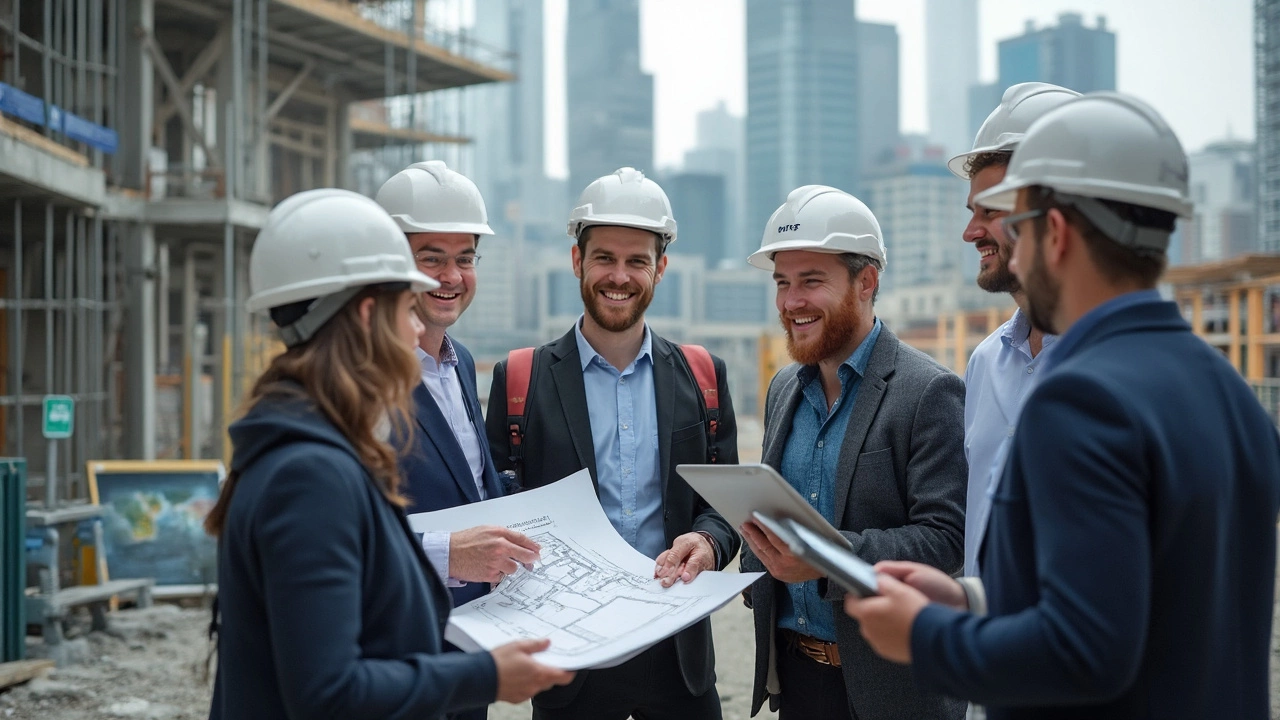
Choosing the Right Construction for Your Project
Picking the right construction type for your commercial buildings isn't about guessing—it's about what fits your needs, budget, and local rules. Start by asking these questions: How tall does your building need to be? Is your budget tight or can you stretch for quality? How fast do you want the project finished? Your decisions here will ripple through the entire project, from design to maintenance costs years down the road.
Steel frame buildings are everywhere for a reason. Want flexible layouts, quick builds, or planning an office tower? Steel lets you go high and wide, and it's pretty easy to run electricity or plumbing later if things change. It's lighter than concrete, so if your build site is tricky—like soft soil or seismic zones—steel usually wins out.
But concrete structures shouldn’t be overlooked. These are perfect when durability and fire resistance matter—a lot of schools, data centers, and hospitals go concrete for safety and low noise. Concrete also handles weight like a champ, making it a go-to for big-box stores or places expecting heavy foot traffic and big equipment.
Here’s a quick head-to-head to help you decide:
Construction Type | Cost Range (per sq. ft.) | Best For | Speed |
---|---|---|---|
Steel Frame | $20 – $40 | Office towers, warehouses, malls | Fast |
Concrete | $30 – $50 | Schools, hospitals, secure facilities | Medium |
If you're in a region where earthquakes or hurricanes hit, check your local building codes—sometimes they require special construction. For example, California pushes for steel and reinforced concrete to handle quakes, while hurricane zones in Florida prefer reinforced concrete with impact windows.
Don’t pick materials alone. Loop in your architect, contractor, and even your future tenants if you can. Sometimes a tiny bit more upfront in the right construction type saves you huge headaches and costs later. And don’t forget about future changes—flexible designs pay off if you might remodel or expand.
Bottom line? Weigh what matters most for your project: cost, speed, long-term durability, and safety. Get real about your priorities—smart upfront choices for your commercial construction type save money and hassle down the line.