Ever been part of a big construction project and felt lost in the sea of workers, managers, and crews, all wearing different company logos? You might have seen trucks with unfamiliar names parked beside major brands. That's the world where lower tier contractors work. Their role is often overlooked, but they keep the gears turning in the massive machine that is commercial construction. These companies or individuals don't usually work directly for the main contractor; instead, they're hired by someone who was already brought onto the project—like a subcontractor hiring another specialist. This complicated human chain can get long and tangled, which leads to all sorts of challenges on the job site and beyond.
Understanding the Role: Who Are Lower Tier Contractors?
Picture a construction project as a layered cake. At the very top sits the client or developer—the person who wants the building done. They hire the main contractor, the one whose name is on the construction fence. That’s your top-tier contractor. But the main contractor can't do everything solo. They bring in subcontractors for plumbing, electrical, foundations, and so on. Now, here’s where the lower tier kicks in: these subcontractors might need extra hands or specialized skills, so they hire more companies or individuals. These are the lower tier contractors—sometimes called sub-subcontractors, second-tier contractors, or even third-tier, depending on how deep you go.
You’ll find lower tier contractors everywhere there's a big job and a need for niche expertise. Think about fire alarm installers, structural steel erectors, commercial HVAC techs, or even companies focused entirely on cleaning services for new builds. A 2023 study from the Construction Industry Institute showed that nearly half of all subcontracted work on large commercial projects is actually carried out by lower tier companies—yet they’re not the ones sitting in project meetings or negotiating directly with the client. Their main point of contact is the subcontractor who hired them, which can make communication tricky when challenges pop up.
Lower tier contractors usually handle “smaller slices” of work, but that doesn’t make them less important. For example, a glass installer might only be responsible for a single floor of windows, but if they delay, it can hold up everything from drywall to painting. Lower tiers are paid by the folks above them, not by the project owner. As a result, their livelihoods depend on both the reliability of those above and how smoothly the entire chain operates.
The paperwork can stack up pretty high. Lower tier agreements often contain strict terms and conditions, and payment lags are a big concern. The UK’s Department for Business & Trade noted in 2024 that about 60% of payment disputes on commercial projects are due to miscommunication or delayed payments between these layers. If you’re a lower tier contractor, you need to be sharp with contracts and invoicing. Some countries, like Australia, even have security of payment legislation specifically designed to protect lower tier companies from getting stiffed.
These contractors might go unnoticed by outsiders, but anyone who manages a job site knows how vital they are. From keeping completion on track to solving tough technical problems, lower tier contractors are often the unsung heroes—though their work environments can be precarious. The more layers, the bigger the risk that information or payments don’t filter down right.
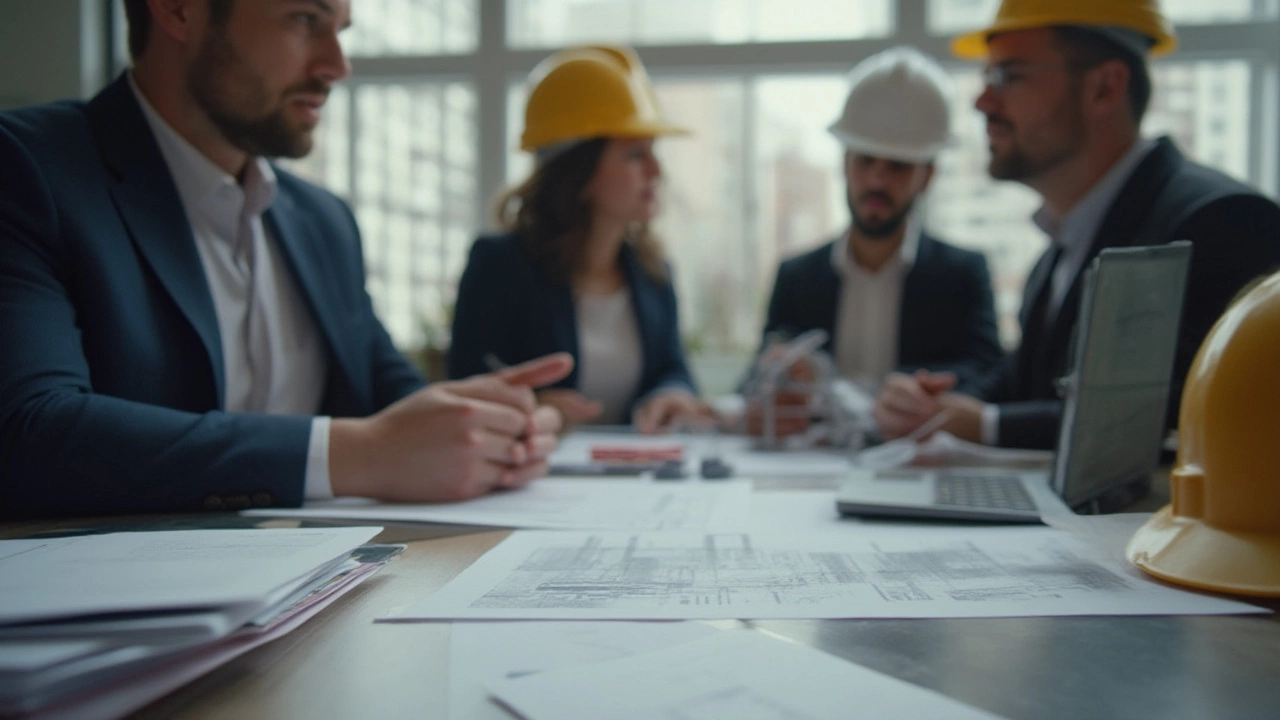
Risks, Legal Realities, and Practical Challenges
It would be nice if construction jobs ran like Swiss watches—smooth, predictable, and perfectly synced. Reality’s messier. Working as a lower tier contractor means you face more risk than most folks higher up the food chain. Why? First, you’re not in direct contact with the main decision-makers. If your hiring subcontractor runs into trouble—budget cuts, bankruptcy, or simple mismanagement—you might be left hanging, both with work and payment. Data from the US Chamber of Commerce’s 2023 Construction Outlook shows that nearly 70% of lower tier contractors have experienced payment delays longer than 60 days. That number spikes even higher on giant multi-million projects.
Then there’s the legal web. Lower tier contracts are usually subcontracts-of-subcontracts, often with clauses that pass down obligations from the main contract. This means if the project owner changes a spec or schedule and the changes don’t reach all the way down the chain, a lower tier contractor might be working off old plans or missing critical information. Some contractors have ended up eating large unexpected costs because they didn’t get proper notification from higher up. UK law, for example, says lower tier contractors can only get what’s been paid out above them—sometimes called "pay-when-paid" clauses—which often cause friction.
Insurance is another headache. While top-tier companies have massive umbrella coverages, lower tier contractors are expected to manage their own risks—think liability, worker safety, and property damage. According to a 2022 industry survey, 40% of lower tier firms reported that a lack of clear safety protocols from those above led to accidents or fines. It’s smart to never just take someone’s word that "all policies are covered." Check what’s in your contract, confirm coverage, and keep proof of everything. Trusted legal or business consultants can be a lifesaver for managing these risks.
One of the most notorious problems lower tier contractors face? Getting information late. Communication breakdowns, even over minor details, cause huge ripple effects. The Construction Management Association found in 2023 that construction projects with more than three subcontractor layers had 2.5 times as many project delays compared to ones with simpler chains. And almost always, lower tier folks bore the brunt of those delays—sometimes without getting paid extra for lost time.
Take this scenario: you're installing insulation, but now the timelines shift because the structural steel crew (another lower tier group) ran late. You’re stuck, labor is idle, equipment is eating up rental costs, and your billings can’t move forward. These kinds of delays also lead to disputes about who pays and who’s on the hook. For lower tier contractors, documenting everything becomes critical—emails, delivery receipts, even photos can help if you need to claim extra costs later on.
Legal trends suggest things are slowly improving. With new requirements for transparent payment schedules and “right to adjudicate” clauses, some countries and US states are making it harder for lower tier contractors to be left out in the cold. Keeping up with these laws and using template agreements from trade associations is smart business. There’s also increased pressure from clients and investors to simplify contracting chains wherever possible—which can mean more opportunities for the most reliable lower tier companies to move up in the food chain.
Here’s a snapshot of common issues lower tier contractors deal with, according to a 2024 industry survey:
Challenge | Reported by (%) |
---|---|
Payment delays | 70 |
Lack of clear contract terms | 55 |
Late design/spec changes | 48 |
Project delays | 40 |
Safety & compliance confusion | 35 |
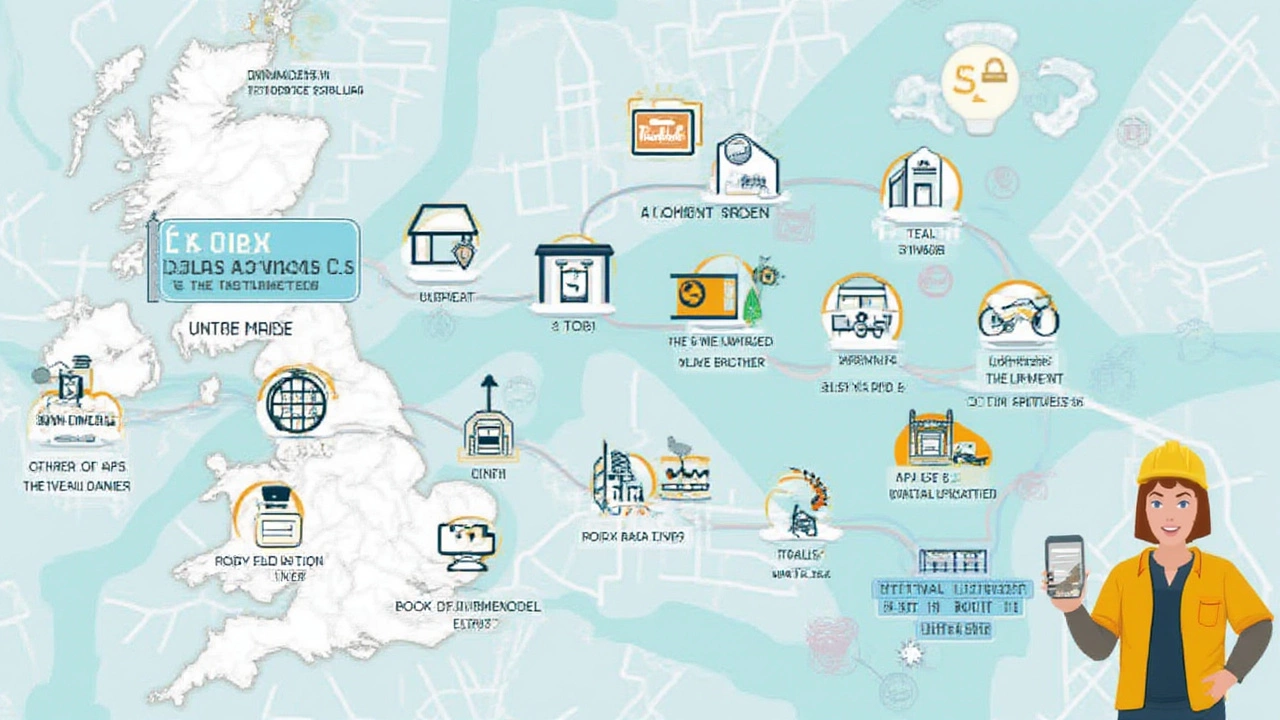
Smart Strategies for Working with Lower Tier Contractors
So, what’s the best way to work with—or as—a lower tier contractor and come out ahead? It starts with understanding the chain of command on every job. Be clear on exactly who you report to, what they expect, and how your work fits into the master schedule. Pro tip: ask for a copy of the full construction program and clarification on your scope before setting a single foot on site.
Contracts matter—sometimes more than the work itself. Standard subcontracts can be shockingly one-sided, so look closely at payment terms, dispute resolution steps, and termination rights. Don’t be afraid to negotiate. Even small wins—like reducing payment lag time or adding clarification on change order approvals—can make your life smoother. Industry bodies such as Associated General Contractors (AGC) offer contract templates specifically meant for lower tier use, and these have far more “teeth” than whatever a hurried superintendent emails over at midnight.
The best lower tier contractors have a reputation for reliability. Show up when you say you will, keep your paperwork neat, and communicate delays or issues the moment they arise. Building this kind of trust gets you invited back, or sometimes asked to bid directly to the main contractor the next time around. Keep records not just for legal reasons, but for learning—tracking what caused hiccups last time can save you grief next project.
For main contractors and project managers, the key is inclusion and clarity. Don’t treat lower tiers as invisible or disposable. Regular all-hands meetings—maybe once a week—help keep everyone informed (and give the quietest contractors a chance to flag brewing problems). Digital management tools are popular now too; platforms like Procore and Buildertrend make it possible to see who’s been briefed, who’s paid, and who’s behind schedule at a glance. Lara always jokes that construction managers secretly love spreadsheets—that digital workflow is their happy place.
If payment is a sticking point, consider project bank accounts, where all parties get paid directly from a central account after milestone approvals. Studies from both UK and Australia show these systems reduce nonpayment claims by more than 50%. Another tip: build buffer time into schedules—if everything goes right, great, but if there’s a delay several layers down, you’ll still finish on time.
If you’re a lower tier contractor looking to grow, aim to pick up extra skills or specialized certifications. Advanced safety training, tech like drone mapping, or even just being able to handle complex paperwork better can make you a standout when main contractors are looking to prune the subcontractor tree. The more reliable you become, the fewer layers there are between you and the top—and, often, the better you’re paid.
And remember—everyone, no matter where they sit in the project hierarchy, wants the building finished on time, safely, and for a fair price. Communication, decent paperwork, and a bit of empathy toward the next layer up (or down) go a long way. Sure, the system isn’t perfect, but the best-run jobs are always the ones where every contractor, from the main to the “lower,” works as part of the same team. That’s when construction feels like something more than just work.