You probably walk past concrete walls, steel beams, and wooden frames every day without a second thought—but there’s a whole story behind why these materials show up on almost every job site. Construction isn’t just about slapping stuff together; the choice of material decides how strong, safe, and comfy your finished building feels.
If you’ve ever wondered why some homes last a hundred years while others crumble after a storm, or why skyscrapers don’t sway in the wind, a lot boils down to what they're made of. Knowing which materials builders count on—concrete, steel, wood, and a handful of others—can save you time, money, and hassle. Each has a sweet spot where it shines, and some pitfalls if you pick wrong.
Stuck on what to use for your garage, home extension, or a backyard shed? There’s no magic universal answer. This article will lay out strengths, weaknesses, and little-known facts about the top ten materials, so you can figure out what works best for your own project—without getting lost in manufacturer brochures or sales pitches.
- Concrete: The Building Block
- Steel: The Backbone
- Wood: Nature’s Classic
- Brick and Blocks: Trusty Sideskicks
- Stone, Glass, and Beyond
- How to Pick the Right Material
Concrete: The Building Block
It’s hard to imagine modern construction without concrete. This stuff shows up everywhere: homes, bridges, schools, even sidewalks under your feet. The secret to concrete’s popularity? It’s tough, easy to shape, and not crazy expensive. You get it by mixing cement, water, sand, and gravel or crushed stone (that mix is called aggregate in the industry). Once it sets, you’re working with something that holds up a multi-story building or parking garage, no problem.
Cement is the glue that binds everything together, but concrete is the whole mix. Fun fact: the Romans were using a kind of concrete around 2,000 years ago, and some of their buildings (like the Pantheon) are still standing. Modern versions are even stronger. Fresh concrete can be poured into pretty much any shape before it hardens, making it great for unusual projects or creative designs.
Here’s what makes concrete a big deal on job sites:
- Durability: It handles harsh weather and heavy loads, which is why you see it in foundations and highways.
- Fire resistance: Concrete doesn’t burn, so it adds a layer of safety to structures.
- Low maintenance: Once it sets, you usually don’t have to do much, besides maybe sealing cracks if they show up.
Of course, concrete isn’t perfect for every job. It can crack if it’s not mixed right or if the ground shifts under it. If you live somewhere that gets lots of freezing and thawing, ask your supplier for the right kind of aggregate—it helps protect against frost damage. Also, regular concrete isn’t great in tension (when something tries to pull it apart), so for things like floors and bridges, rebar or mesh gets added to make it way stronger.
Tip: If you’re pouring concrete for a driveway or patio, pay attention to curing times. Don’t rush. Concrete takes days, sometimes weeks, to reach full strength. The longer it cures, the tougher it gets.
Steel: The Backbone
If you look up at any city skyline, you’re staring at a whole lot of steel. There’s a simple reason for that: steel delivers unmatched strength and flexibility, letting architects push the limits. Skyscrapers, bridges, sports stadiums—they all owe their weird shapes and record-breaking heights to steel’s muscle.
"Steel has revolutionized construction. Without it, our modern cities would look nothing like they do today," says Professor John Bell, a structural engineering expert from the University of Manchester.
It’s not just about brawn, though. Steel is surprisingly lightweight for how tough it is. It’s easy to move, shape, and connect, so construction moves way faster compared to older materials. And while wood burns and concrete cracks, steel stands up to fire, wind, and earthquakes—just check the numbers:
Property | Steel | Concrete | Wood |
---|---|---|---|
Tensile Strength (psi) | 36,000+ | 400 | 7,000 |
Fire Resistance | Excellent | Good | Poor |
Longevity | 50-100 years | 50-100 years | 20-50 years |
Steel’s biggest plus? It’s almost endlessly recyclable. Buildings come down, but steel beams go right into the next bridge, warehouse, or rollercoaster. In 2023, over 70% of new steel in the U.S. was made from recycled scrap. If you care about the planet or just your bottom line, that’s huge.
But it’s not all good news. Steel can rust if it’s not treated or kept dry, so any project near the ocean or with lots of rain needs extra coatings or special alloys. And in smaller home projects, steel might be overkill—wood usually wins for sheds, small houses, or cabins.
- Tip: If you want to build fast and go tall, steel is your best bet.
- Tip: Always check for galvanizing or rust-proof coatings if your project is near water.
For most big jobs, steel is the backbone. It gives you speed, safety, and the option to change things later—say, adding a couple more floors or shifting a wall down the road. No other construction materials offer that mix of flexibility and brute force.
Wood: Nature’s Classic
For centuries, wood has been a go-to in building, and honestly, it’s easy to see why. It’s everywhere—houses, cabins, sheds, even entire apartment buildings. Most folks like working with wood because it's strong for its weight, easy to cut or shape, and surprisingly good at handling both heat and cold. In some climates, it can last for decades if you keep moisture and bugs away.
Not all wood is the same, though. You’ll run into softwoods like pine and fir in framing and roof trusses, mainly because they’re cheap and grow fast. Then there’s hardwoods—think oak, maple, or cherry. They’re pricier, but also tougher, so builders usually save them for flooring, doors, or furniture, where looks and wear matter more.
One thing to remember with wood: it needs protection. Without paint, sealant, or pressure treatment, wood is a magnet for rot and termites. That's why outdoor decks and fences use treated lumber—it holds up better when it rains cats and dogs. If you’re on a tight budget, untreated wood might be tempting, but you’ll likely spend more fixing or replacing it down the line.
Here are some smart tips when picking wood for a project:
- Check for straightness—warped boards can turn your walls or floors into a wavy mess.
- Pick the right grade—structural framing needs stronger grades, while trim or paneling can get away with fewer knots and blemishes.
- If it’s touching the ground or gets wet, demand pressure-treated lumber or naturally rot-resistant stuff like cedar.
- Always store your wood out of rain and direct sun to keep it from twisting or cracking before you use it.
Compared to materials like steel or concrete, wood gives you a warmer look and is usually easier to swap out or repair. Plus, trends are swinging back toward wooden houses for good insulation and eco-friendliness, especially when the wood comes from responsible sources. Just be ready to do a little maintenance, and you’ll get years of solid service out of it.
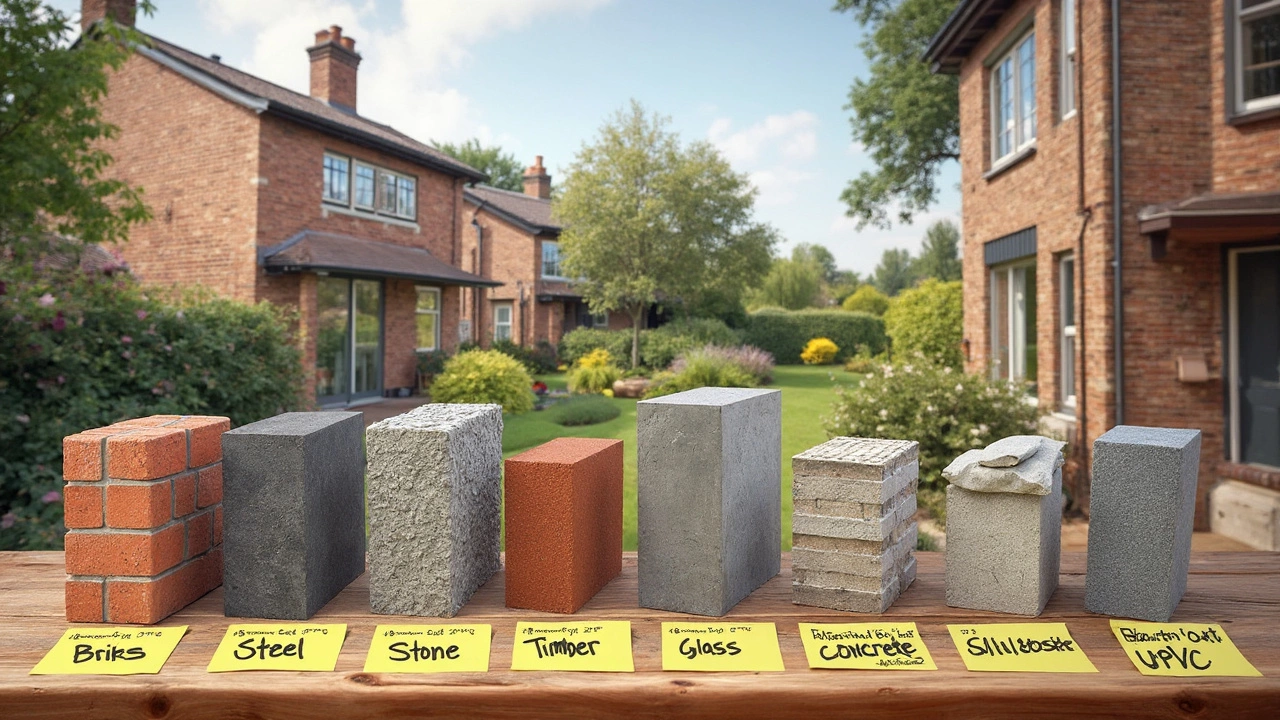
Brick and Blocks: Trusty Sideskicks
Bricks and blocks might not seem flashy, but they do the heavy lifting on almost every street. For centuries, people have used bricks for everything from cozy fireplaces to entire neighborhoods. These materials are all about reliability—they keep buildings standing for decades and shrug off bad weather if you build them right.
Not all bricks and blocks are the same. You’ve got clay bricks, concrete blocks, fly ash bricks, and more. While old-school red clay bricks still pop up in home builds, concrete blocks are stealing the show for bigger projects thanks to their size, strength, and speed of installation. One big plus: using blocks can cut down the time to build a wall by half compared to laying old-fashioned bricks.
The secret sauce here is in the way these materials lock together. Their size, shape, and even little holes or grooves mean they stay put—no fancy adhesives needed except some good mortar. Fire? Not a big worry. Termites? Not interested. Flood or high winds? Brick and block walls can take a beating and keep going. But they are heavy, and unless you reinforce them (if you’re in an earthquake zone, check your local code), they can crack under stress.
- If you want soundproofing, brick and block walls perform way better than thin wood or drywall.
- Thinking green? Fly ash bricks use industrial waste and cut down on carbon footprints.
- On a budget? Concrete blocks cost less per square foot compared to many other wall materials.
- Speed matters? Using bigger blocks or hollow blocks can get you to the finish line faster.
Check out how these options stack up for basic construction materials needs:
Type | Main Use | Strength (MPa) | Fire Resistance | Notes |
---|---|---|---|---|
Clay Brick | Houses, walls, patios | 10-20 | Very High | Classic look, good insulator |
Concrete Block | Large walls, foundations | 3-7 | High | Faster to lay, cost-efficient |
Fly Ash Brick | Eco-friendly builds | 7-10 | High | Lower carbon impact |
One last tip: Always check what’s recommended in your region—cold weather, flood risks, or frequent earthquakes can change what works best. Sometimes, combining blocks and bricks in one build gives you the perks of both. Just be sure the final wall lines up with your needs, and you’re set.
Stone, Glass, and Beyond
Stone has a rep for being ancient, but it’s far from outdated. Granite, marble, and limestone all pop up in homes, malls, and even airports. Why use stone? It’s sturdy, lasts nearly forever, and you almost never have to worry about pests or rot. Granite countertops, anyone? On exteriors, stone adds curb appeal and stands up to wild weather better than most other materials.
Glass, on the other hand, totally changed how buildings look and feel. Think of the nearest city skyline—almost every modern office or condo uses glass for those massive windows and sleek facades. Double or even triple-glazed glass isn’t just see-through; it locks in heat or AC, cuts down outside noise, and lets in loads of light without the UV damage. Smart glass can even change shade on demand, which is great for saving on energy bills and avoiding those awkward sun glares.
If you’re wondering how these stack up against each other, check this out:
Material | Main Use | Strength | Thermal Performance | Average Cost (USD/ft²) |
---|---|---|---|---|
Granite | Countertops, Walls, Flooring | Very High | Excellent | $40–$100 |
Glass | Windows, Facades, Railings | Medium | Good (if insulated) | $15–$50 |
Limestone | Walls, Facades, Pavers | High | Moderate | $10–$30 |
It doesn’t stop with stone and glass, though. Fiber cement, modern plastics, and even clay tiles are finding a spot alongside the classics. Fiber cement, for example, won’t catch fire, shrugs off insects, and handles crazy weather with ease—all reasons why it’s getting popular for siding. Plastics are cheap and versatile, especially for plumbing and insulation, but just keep an eye on heat resistance and lifespan.
When picking from these options, try to match the material to the job. Stone's a workhorse for areas that take a beating, like driveways or commercial fronts. Glass is your go-to when you want style and light, and don’t forget about those extra energy savings. For something low-maintenance and tough, fiber cement is hard to beat. No material is perfect, so weigh what matters most: looks, cost, strength, or energy use. Your choices can affect your comfort, your wallet, and even the planet, so it pays to think it through.
Keep in mind, no project is too small for smart material choices. Even a garden shed or sunroom can benefit from picking the right construction materials for the job.
How to Pick the Right Material
Walking into a store or talking with a supplier can get overwhelming with options. Every project doesn’t need the strongest or most expensive stuff—sometimes lighter, cheaper, or faster-to-install makes more sense. So how do you actually decide what to use? It all comes down to asking the right questions and looking at the facts, not the sales talk.
Here’s a straightforward checklist that every builder or DIY-er should keep in mind before buying anything:
- Construction materials need to match the load or weight your project will handle. For example, concrete handles heavy loads, while wood can't take as much pressure over long spans.
- Weather is huge—Will your project face lots of rain, wild temperature swings, or salty air? Steel can rust fast by the coast unless it’s protected, while treated wood can hold up for decades outdoors.
- How fast do you need it done? Some materials, like precast concrete or steel panels, speed up builds when time matters.
- Don’t ignore your budget. Some options look shiny on brochures but can eat up cash fast. There’s usually a practical middle ground if you check prices and labor costs.
- Safety counts. Think about fire resistance (concrete and brick are great here), earthquake zones (steel frame wins every time), and indoor air quality (go for low-VOC products).
- What’s the future—are you going to expand, remodel, or take things apart later? Steel bolts come off, but concrete’s there for good.
Here’s a quick data table to give a snapshot of how common materials stack up by strength, cost, and speed to build:
Material | Main Use | Average Cost ($/sq.ft.) | Build Speed | Strength | Weather Resistance |
---|---|---|---|---|---|
Concrete | Foundations, floors | 5-10 | Medium | High | Excellent |
Steel | Frames, high-rises | 11-18 | Fast | Very High | Good (needs protection) |
Wood | Houses, interiors | 6-8 | Fast | Medium | Fair (treated is better) |
Brick | Walls, facades | 8-12 | Slow | High | Excellent |
Stone | Exteriors, patios | 12-20 | Slow | Very High | Outstanding |
If you’re not sure, ask a contractor or architect—don’t just copy what your neighbor did. And when in doubt, double-check building codes. They’re there for a reason and can save lots of headaches later. Remember, the best choice isn’t always the fanciest or the oldest; it’s what makes sense for your goals, location, and wallet.