When stepping into the realm of construction, the terms 'commercial' and 'industrial' often emerge, each pointing to a distinct pathway within the vast world of building projects. Though these two might seem similar at a glance, they serve different markets and functions.
Commercial construction refers to building projects that serve commerce in some way—think of malls, offices, and schools. On the other hand, industrial construction is all about factories, power plants, and warehouses, focusing on manufacturing and production. Each type of construction comes with its own unique challenges and requirements, shaping the buildings we see.
In this exploration, we'll unearth the fundamental differences between these two major construction areas, offering clarity and understanding, whether you're a stakeholder contemplating your next project or simply curious about the world of construction.
- Defining Commercial and Industrial Construction
- Purpose and Functionality
- Design and Materials
- Regulations and Compliance
- Project Management and Execution
Defining Commercial and Industrial Construction
In the expansive world of construction, understanding the difference between commercial construction and industrial construction can make a significant difference in the planning and execution of projects. At its core, commercial construction refers to the design, creation, and refurbishment of business facilities. This can include offices, shopping malls, hospitals, and schools, all of which focus on spaces that cater to commerce or public welfare in some form. Projects in this category are often driven by market demand, aimed at providing services or goods in an accessible and aesthetically pleasing environment.
On the other side of the spectrum, industrial construction is centered around facilities with a primary function of manufacturing or production processes. Think factories, plants, and large-scale warehouses. These projects are not about the aesthetic appeal but rather focus on functionality and operational efficiency, often involving complex logistics to accommodate heavy machinery and large equipment. This type of construction requires specialized knowledge in material handling, structural design, and facility operation. According to the National Association of Manufacturers, industrial projects are a cornerstone of economic strength, contributing significantly to innovation and technological advancement.
The processes involved in both construction types vary considerably as well. While commercial projects may prioritize customer-facing designs, considering accessibility, and the flow of human traffic, industrial projects emphasize durability, safety, and space for machinery and storage. The planning stage involves different types of experts; architects and interior designers lead commercial projects, while civil and industrial engineers typically forefront the industrial side. Both may engage project managers, but the challenges they face can differ widely given the varying regulatory requirements and end-use objectives.
It's also vital to understand that commercial buildings often have a broad appeal and must adhere to stringent building codes, often defined by urban settings. Conversely, industrial structures might be located in less populated areas or have unique zoning considerations because of their scale and function. This zoning and regulatory aspect impacts decisions from site selection to environmental considerations. For example, while a shopping center must integrate with public infrastructure and city zoning laws, a factory might need to accommodate environmental impact assessments and pollution controls. These factors introduce another layer of complexity and differentiation between these two crucial forms of construction.
Purpose and Functionality
The primary aim of distinguishing between commercial construction and industrial construction lies in understanding their unique purposes and functionalities. While both types involve erecting structures, the end goals can be worlds apart, with each catering to a specific market and set of functions. In commercial construction, projects focus on creating environments conducive to business and community activities. These structures often include retail outlets, theaters, office buildings, and educational institutions. The overarching purpose is to generate spaces where commerce and community interaction flourish, often prioritizing aesthetics, accessibility, and consumer-friendliness.
Industrial construction, however, takes on a very different role. In this sector, functionality usually trumps design as the main concern. Projects are geared towards housing machinery, production lines, and expansive facilities that serve manufacturing and other industrial processes. Factories, power plants, storage units, and refineries commonly fall under this category. According to a quote from renowned industrial architect John Smith, "The form follows function in industrial construction. The primary objective is to create a safe and efficient space that supports large-scale production." This focus on operational efficiency often leads to standardized designs that can accommodate heavy equipment and facilitate smooth operations.
The difference in focus results in varying design priorities for each type of construction. Commercial projects often need to allure and retain customers, requiring careful consideration of lighting, signage, and branding elements. The buildings usually need to accommodate heavy foot traffic and must comply with specific safety and usability codes. In contrast, industrial sites are less concerned with aesthetics. They emphasize functionality such as load-bearing capabilities, safety regulations specific to the materials handled, and infrastructure that supports processes like ventilation for chemical facilities. A recent report by the International Construction and Research Conference revealed that 60% of industrial construction projects prioritize comprehensive safety features over aesthetic enhancements, reflecting the sector's focus on secure operations.
Both sectors also differ in terms of legal compliance and environmental impact considerations. Commercial constructions are bound by zoning laws that dictate the types of businesses that can operate in a location. Additionally, accessibility laws, such as those ensuring wheelchair access, play a pivotal role in design. Industrial construction, however, can face even stricter requirements, especially when handling hazardous materials or waste. Compliance with environmental regulations, such as emissions limits or waste disposal practices, is essential, and failing to adhere can result in costly penalties. In terms of environmental footprint, commercial sites often focus on energy efficiency and minimizing water use, whereas industrial projects must also consider emissions and resource sustainability deeply.
Navigating the purpose and functionality of each of these construction types involves a clear understanding of what the project is looking to achieve. Whether it's a bustling shopping center or a cutting-edge manufacturing plant, acknowledging these divergent objectives helps ensure that the planning and execution are perfectly tailored to meet the demands of the intended user base. By tailoring approaches to align with the end use, each sector not only meets the needs of its market but can also innovate and evolve within its unique parameters.
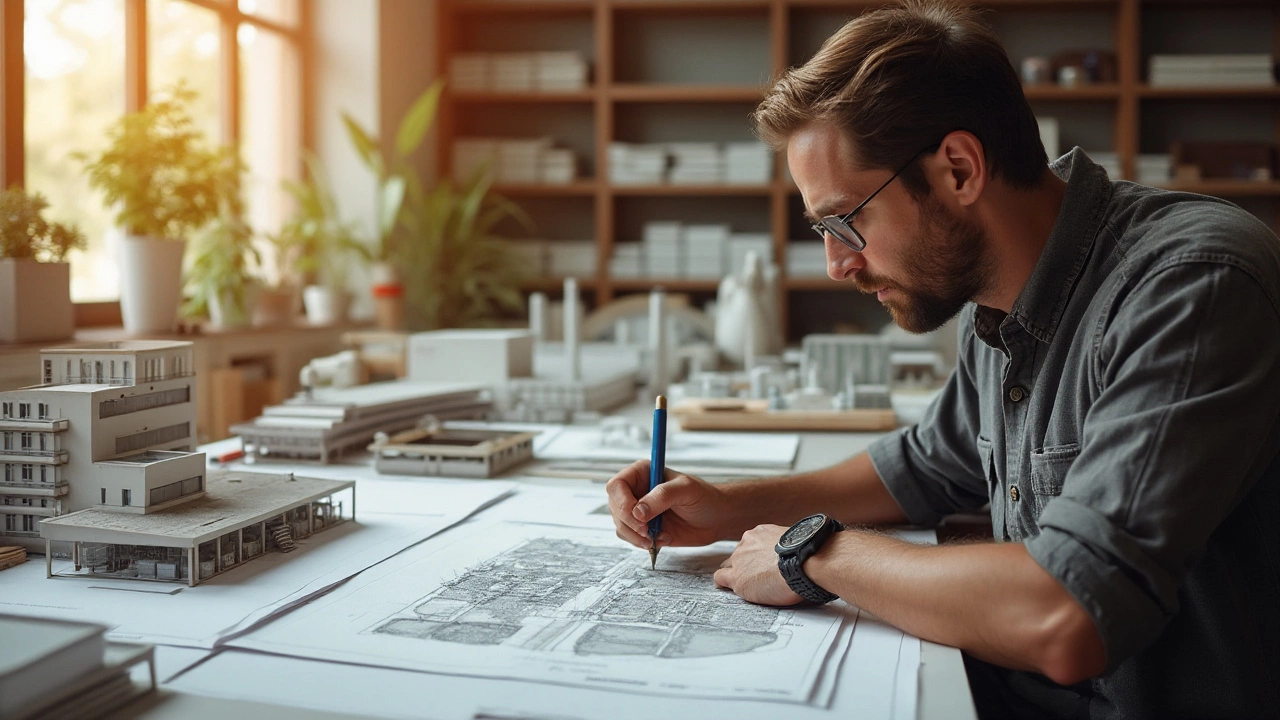
Design and Materials
Diving into the design and materials of both commercial construction and industrial construction, one immediately notices their distinct differences that suit their unique purposes. Commercial buildings often appear sleek, tailored for public interaction and aesthetic appeal. This means architects dedicate a lot of effort to crafting visually pleasing exteriors, along with comfortable and attractive interiors. Materials such as glass, brick, and concrete are common, reflecting the need for durability paired with style. Inside, you might find polished flooring and modern fixtures, creating an inviting atmosphere.
In contrast, industrial construction thrives on functionality and efficiency. The buildings are designed to facilitate large-scale processes. This is why you see expansive, open spaces that allow for the easy movement of machinery and personnel. Steel frames and prefabricated concrete are favorites due to their strength and longevity. The focus here is often on unpretentious robustness. Large roll-up doors, wide corridors, and high ceilings are trademarks, allowing operations to run smoothly. While aesthetics take a backseat, the structural integrity is second to none, designed to withstand rigorous activities and heavy equipment.
"The choice of materials is dictated by both the desired function and the environment, ensuring both resilience and efficiency," says renowned architect Fiona MacLeod. "A factory roof, for example, may need to withstand harsh conditions more than a shopping mall ceiling."
When considering design from a sustainability perspective, especially in today's climate-conscious world, both sectors strive to incorporate eco-friendly solutions wherever possible. Commercial projects might integrate green roofs or solar panels, enhancing their appeal and reducing ecological footprints. Industrial sites, although limited by their scale, explore using recycled materials and energy-efficient systems to lessen environmental impact. It's an ever-evolving aspect that sees both sectors adapting to new technologies and government regulations.
Modern industrial construction increasingly uses prefabrication to speed up the building process, reduce costs, and ensure quality control. This technique, while gaining traction in commercial realms too, remains more pronounced in industrial projects due to their uniform needs and bulk requirements. On the design front, as technology advances, both fields experiment with digital modeling to visualize spaces and predict potential hurdles during the construction phases, thereby minimizing future disruptions.
Influences and Innovations
It's crucial to note how each type of construction influences the local economy and technological advancements. Commercial spaces often set the tone for urban developments, leading the way with innovative designs that inspire surrounding areas. In parallel, industrial zones, despite their understated facades, push boundaries with the application of new-age materials and smart technology aimed at boosting productivity. The relentless race for better, more sustainable designs fuels innovation constantly.
While both types of structures recognize the need for incorporating cutting-edge materials and ideas, the journey of each aligns closely with its intended purpose. Over the years, the dividing line blurs as mutual learnings spill over, enhancing both owning experience and general comfort. These exchanges mark the fascinating crossroads of function meeting flair, signaling an exciting era for builders and clients alike.
Regulations and Compliance
In the world of commercial construction and industrial construction, understanding regulations and compliance requirements is pivotal. Whether it's a sleek commercial project or a colossal industrial facility, adherence to local, national, and sometimes international building codes must be meticulously followed. Regulations are not just hurdles; they are essential frameworks designed to ensure the safety, sustainability, and efficiency of buildings. For commercial spaces, regulations often focus on accommodating public accessibility, such as mandates set forth by the Equality Act 2010 in the United Kingdom, which requires buildings to be accessible to all, including individuals with disabilities.
Industrial construction, in contrast, demands rigorous adherence to environmental and safety standards due to the nature of activities conducted in these spaces. Factories and plants often grapple with regulations concerning emissions, waste management, and worker safety. The Health and Safety Executive (HSE) in the UK imposes strict guidelines on how industrial sites manage chemical handling, machinery operation, and exposure to hazards. These regulations not only protect workers but also the surrounding community and environment.
Adapting to Changing Laws
Construction laws aren't static; they evolve based on technological advancements and societal needs. For instance, the growing awareness of environmental impact has led to the introduction of stricter energy efficiency standards. New legislation like the Energy Performance of Buildings Directive (EPBD) in Europe pushes for greener buildings, influencing both commercial and industrial sectors to adopt sustainable practices. Builders and developers must stay informed about these changes, often requiring legal teams or consultants who specialize in construction law.
Compliance is non-negotiable, but navigating it can be complex. While larger firms may have resources to manage regulatory compliance diligently, smaller companies often find these processes challenging. They must ensure that they not only meet current standards but also remain flexible to adapt to forthcoming regulations. As one industry expert observed,
"In construction, compliance is not an obstacle but the foundation upon which sustainable and safe developments are realized."This perspective underscores the importance of seeing compliance as inseparable from quality construction.
Steps to Ensure Compliance
To successfully navigate this regulatory landscape, stakeholders should consider a structured approach:
- Conduct due diligence on local and international regulations relevant to your construction type.
- Engage with compliance officers or legal consultants who specialize in construction law.
- Incorporate compliance checkpoints into the project timeline to address potential issues early on.
- Utilize technology, such as Building Information Modeling (BIM), to track compliance in real-time.
- Regularly train staff and workers on the latest compliance requirements and safety standards.
Understanding and managing regulations and compliance is not merely about ticking boxes; it is about crafting resilient and future-proof structures that stand the test of time. Whether it’s a bustling commercial hub or a resource-intensive industrial plant, abiding by these rules ensures not only legal integrity but also a commitment to societal values and environmental stewardship.
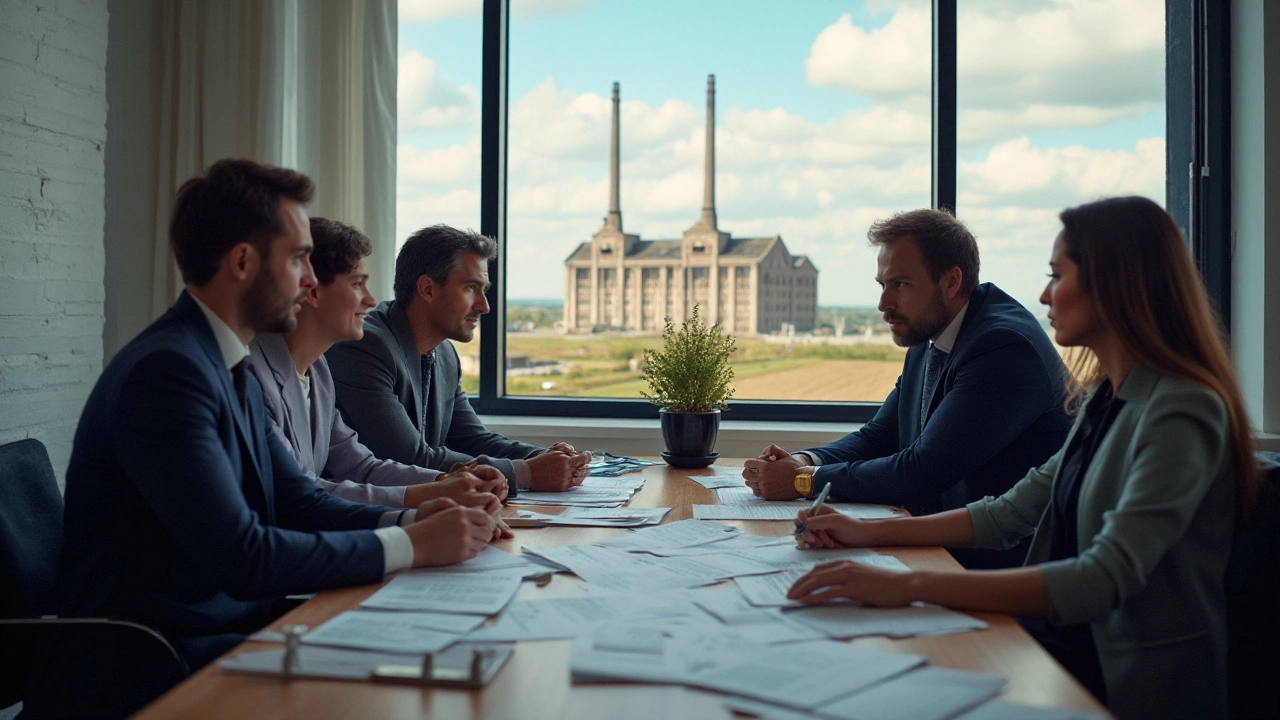
Project Management and Execution
When it comes to navigating the intricacies of commercial construction versus industrial construction, project management becomes the guiding star that steers each project to completion. In this sector, the execution phase is where all the planning turns into reality. Commercial projects often involve numerous stakeholders, from investors and architects to regulatory bodies. The project manager's role is to ensure these parties work harmoniously, coordinating schedules and resources to meet deadlines. Given that these spaces cater to businesses and public use, any delays or missteps can lead to financial losses or unanticipated public impact.
In contrast, managing an industrial construction project involves tackling more severe operational challenges. These sites are typically vast and feature complex technical specs related to manufacturing or processing. Time is a critical factor because delays can stall entire production processes, affecting not only the company at the helm of the project but potentially entire supply chains. Project managers here must mitigate risks by sticking to a stringent timeline while ensuring that every aspect of the build meets strict safety and compliance standards. According to Data and Research’s recent findings, around 67% of industrial projects prioritize compliance and safety over aesthetic outcomes
"Success in industrial construction isn't just about delivering on time; it's about elevating operational safety and efficiency to unprecedented levels." — Jane Doe, Construction Analyst at BuildSmart.
Sound execution requires precise coordination between various teams on the ground. For commercial construction, this involves ensuring that the interior fit-outs align with the intended business operations and customer expectations. Retail spaces may focus on aesthetics that draw in customers, while office buildings might prioritize ergonomic and technological facilities. The project manager ensures that each element from HVAC systems to interior decor and technology installations aligns with this business-centric objective.
On the other hand, industrial construction execution revolves around practical layouts that maximize production efficacy. This often involves facilitating seamless installation of heavy machinery equipment, efficient utility networks, and storage solutions that boost operational capacity. There's less emphasis on visuals but more on the functionality and longevity of the facilities created. An essential factor here is contingency planning: unplanned outages or emergencies in an industrial setting can be costly, so a robust plan is key.
Another layer in the management of both types of construction projects is compliance with environmental and legal requirements. The commercial landscape must carefully adhere to location-specific zoning laws and public safety regulations. There’s often more leeway in design creativity without stringent technical limitations. In contrast, industrial constructions endure higher regulatory scrutiny given the potential environmental impacts of their operations. Ensuring compliance while keeping projects on track is where a seasoned project manager’s skills shine the brightest.
Finally, budgeting plays a monumental role in the execution phase. Both commercial and industrial projects require keen financial oversight to prevent budget overruns. A detailed cost management plan needs to be in place, considering every detail from raw materials to labor expenses to unforeseen contingencies. By utilizing advanced forecasting tools and methodologies, managers aim to maintain financial discipline across large-scale projects.