When delving into the world of construction, understanding different classifications can make a significant difference in how a project is approached and executed. Type C construction represents one of these classifications, characterized by its own unique set of guidelines and material usage, particularly in the realm of commercial buildings.
Type C construction is commonly associated with buildings that have lesser fire resistance needs. That's not to say safety is compromised; rather, it uses different methods and materials to achieve a practical balance of safety and efficiency.
Incorporating Type C standards can not only streamline construction processes but also offer opportunities for creativity in design, as architects and builders work within its parameters. Knowing what Type C entails allows for informed decisions when planning your next commercial building project.
- Defining Type C Construction
- Key Characteristics and Standards
- Materials Used in Type C Construction
- Impacts on Design and Safety
Defining Type C Construction
In the landscape of commercial development, understanding the various building classifications is vital, allowing professionals to navigate regulations and optimize structural integrity effectively. When we delve into Type C construction, it is defined primarily by its specific fire safety requirements and structural capabilities. Unlike Type A and B, which demand more extensive fire resistance measures, Type C offers a more flexible approach, ideal for buildings where occupancy and function permit reduced fire resistance.
This type of construction is part of the International Building Code (IBC) classification system, which standardizes the minimum safety, health, and general welfare requirements for buildings across participating jurisdictions. The IBC's categorization is based on how a building would perform in the event of a fire: Type C structures are considered of very low hazard due to their simplified compliance method. For example, single-story retail complexes or small office buildings often fall under this classification. This allows for innovative design approaches while maintaining a strong adherence to essential safety standards.
One of the critical characteristics of this construction type is the flexibility in the choice of materials. Builders can incorporate a range of products including wood, steel, and masonry, provided they meet the non-combustible standards for the exterior walls. Interestingly, while the perimeter may need to be robust, the interior can often have a relaxed specification, allowing for both expedited construction timelines and creative interior design. This type of versatility doesn’t just cater to aesthetic variety but can significantly cut down on costs without sacrificing compliance.
It's fascinating to note that fire safety regulations, though more lenient, still implement various passive fire protection systems that enhance the overall safety of Type C construction. These can include aspects like smoke alarms, fire retardant treatments for wood, and strategically placed exits to facilitate evacuation in emergencies. According to the National Fire Protection Association (NFPA), buildings classified as Type C have been statistically shown to have a decreased frequency of fire-related incidents when adequately maintained and monitored. These statistics underpin how effective the mix of prescribed construction materials and safety installations can be in preventing disaster.
As contemporary architectural demands evolve, Type C construction continues to be relevant, especially in urban and suburban areas where high-density development faces economic constraints. By understanding its definition within the IBC, stakeholders from architects to developers can ensure their projects not only meet but also creatively exceed safety and usability norms. For buildings where innovation intersects with practicality — and where cost management meets creative expression — Type C is a compelling choice that many professionals are beginning to embrace.
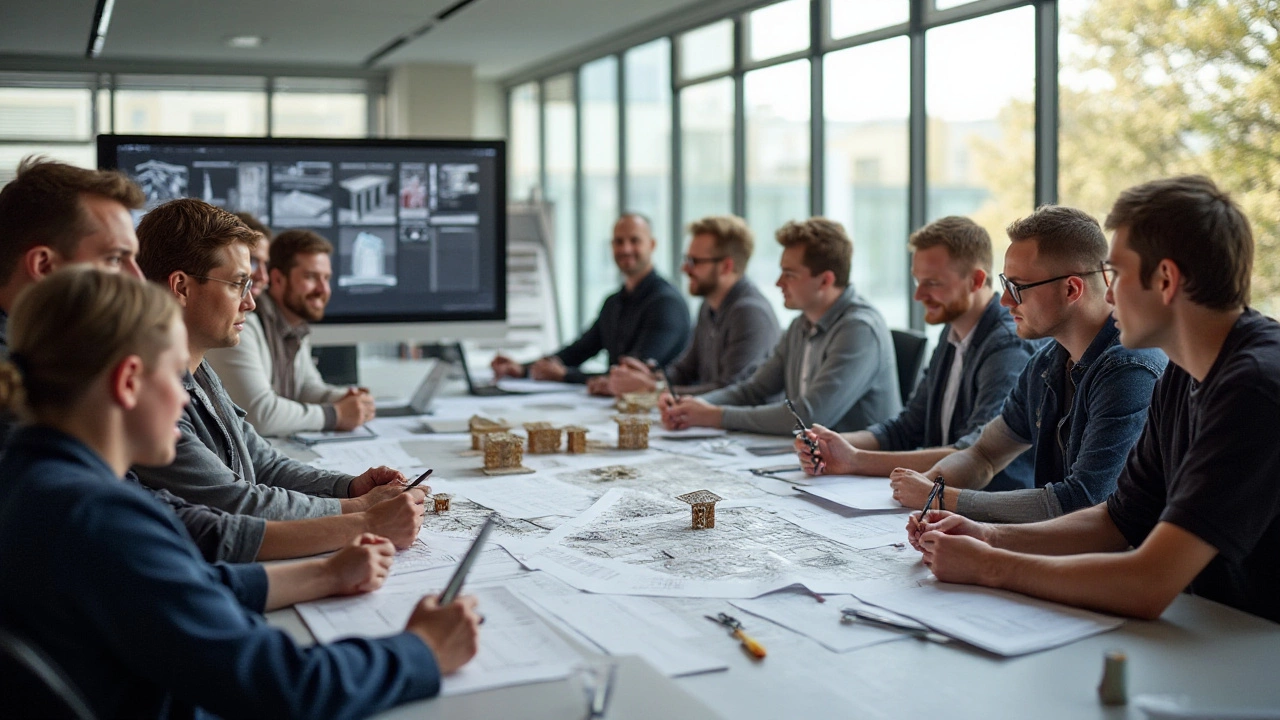
Key Characteristics and Standards
In the realm of commercial construction, understanding the specific characteristics and standards of Type C construction is essential. These standards predominantly address the specific fire-resistance requirements and the range of materials that can be used. Type C is typically associated with low-rise buildings and some residential structures, where fire safety is managed differently than in higher occupancy or more complex architectural designs. The allowance of more common building materials without compromising safety makes it an attractive option for commercial developers seeking cost-effectiveness without sacrificing function.
One significant characteristic of Type C construction is the emphasis on economical yet durable materials. For example, wood framing is permissible under this classification, which makes it an attractive choice for many construction projects thanks to its affordability and versatility. However, certain materials are still required to meet a basic level of fire resistance, ensuring regulations are adhered to even when using less fire-resistant materials. The prescribed methods for testing and maintaining fire-resistant features vary, making it critical to remain informed and up-to-date with evolving standards.
A vital part of Type C construction's standards involves the maximum allowable height and floor area for a given building, which are often less restrictive compared to other construction types. This category generally targets buildings with fewer than six stories, providing leeway in both design and construction approaches. The looser restrictions can, however, require additional considerations when it comes to designing fire egress and integrating fire suppression systems, which are essential to meet safety compliance.
Incorporating the specific characteristics and standards of Type C construction allows builders to craft unique designs that are both beautiful and functional, all while managing to keep costs lower than in more rigorously regulated construction categories. By comprehending the ins and outs of these standards, industry professionals can make more nuanced decisions that benefit the project, the environment, and, ultimately, the end users. As renowned architect Frank Gehry once stated, "Your best work is your expression of yourself. Nowhere is this more true than in the built environment." Thoughtfully adhering to the standards of Type C construction can enhance creativity while still achieving the crucial goal of safety and functionality.
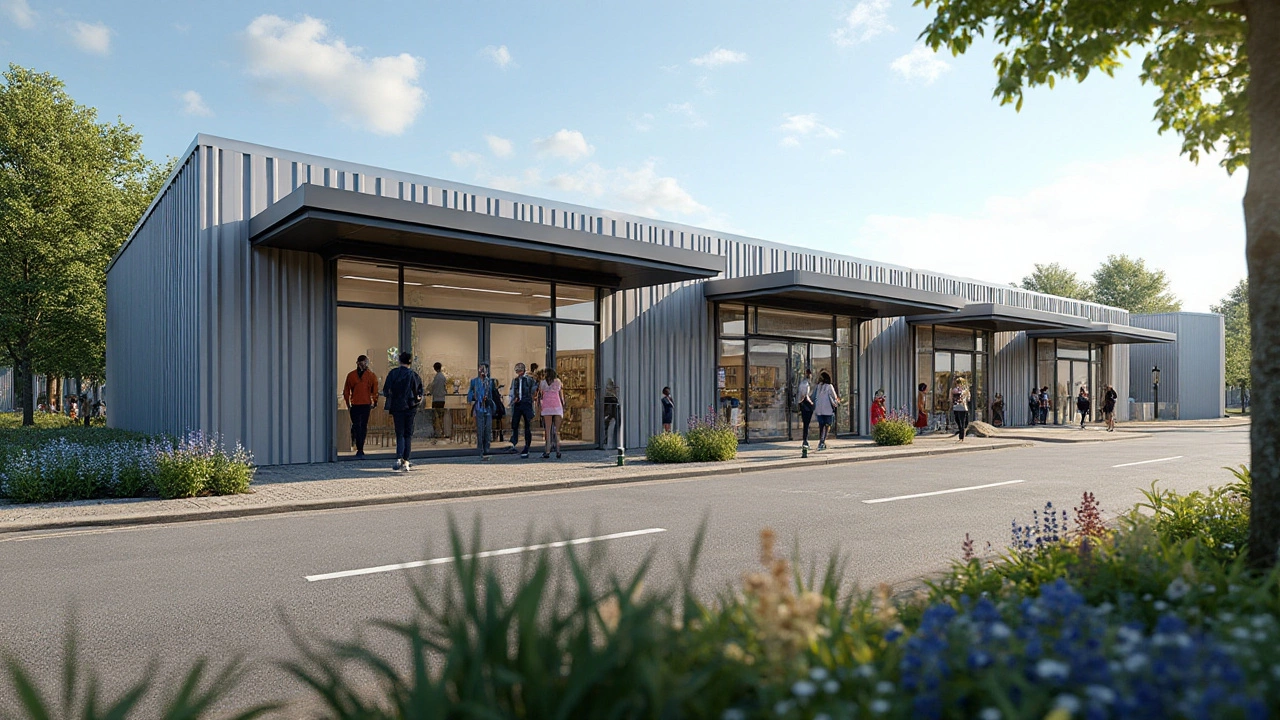
Materials Used in Type C Construction
In the nuanced world of building classifications, Type C construction stands out for its adaptability and cost-effectiveness, particularly in commercial settings. This type of construction tends to utilize materials that strike a balance between cost and functional safety, making it an appealing choice for certain projects. The materials used are varied, yet each serves a distinct purpose in meeting the necessary construction codes without placing undue financial strain on developers.
One of the most prevalent materials in Type C construction is wood. Wood is selected for its versatility and workability, allowing builders to mold it into a variety of shapes and forms as required by the design. It also acts as an excellent insulator, contributing to energy efficiency within the building. Despite the concerns regarding its fire resistance, treated wood products can satisfy the required safety standards, especially if combined with advanced fire-retardant treatments.
Metal components, such as steel, also play a significant role but often in a secondary capacity compared to higher classifications like Type I and II. Steel is commonly found in structural beams and reinforcements because of its strength-to-weight ratio. For commercial construction, this offers the dual benefits of durability and flexibility, as metal structures can withstand substantial pressure and adapt to changing architectural demands.
"Balancing cost-efficiency and safety is the hallmark of smart construction," says James Mitchell, a renowned structural engineer specializing in urban design projects. "Type C Builders have a unique opportunity to innovate by strategically using varied materials while adhering to the prescribed norms."
The integration of lightweight concrete panels is another hallmark of Type C construction, providing the structure with both sound insulation and fire resistance. While they may not possess the same level of fireproofing as those used in Type I and II, these panels help in creating a safe working environment. Meanwhile, drywall, familiar for its cost-effectiveness and ease of installation, continues to be a staple element, offering partition solutions within the building’s interior.
Modern advancements have also brought about the increased use of composite materials. These innovative products often combine synthetic and natural resources to create materials that boast high resilience and adaptability. These composites can be tailored to specific needs, integrating the positive traits of different components to enhance the building's overall performance.
Every material chosen in Type C construction contributes to a larger goal: creating structures that are both economically viable and compliant with safety codes. As architects and engineers gain more freedom within this classification framework, the amalgamation of traditional and contemporary materials creates endless possibilities for commercial buildings that are not only functional but also innovative and appealing.
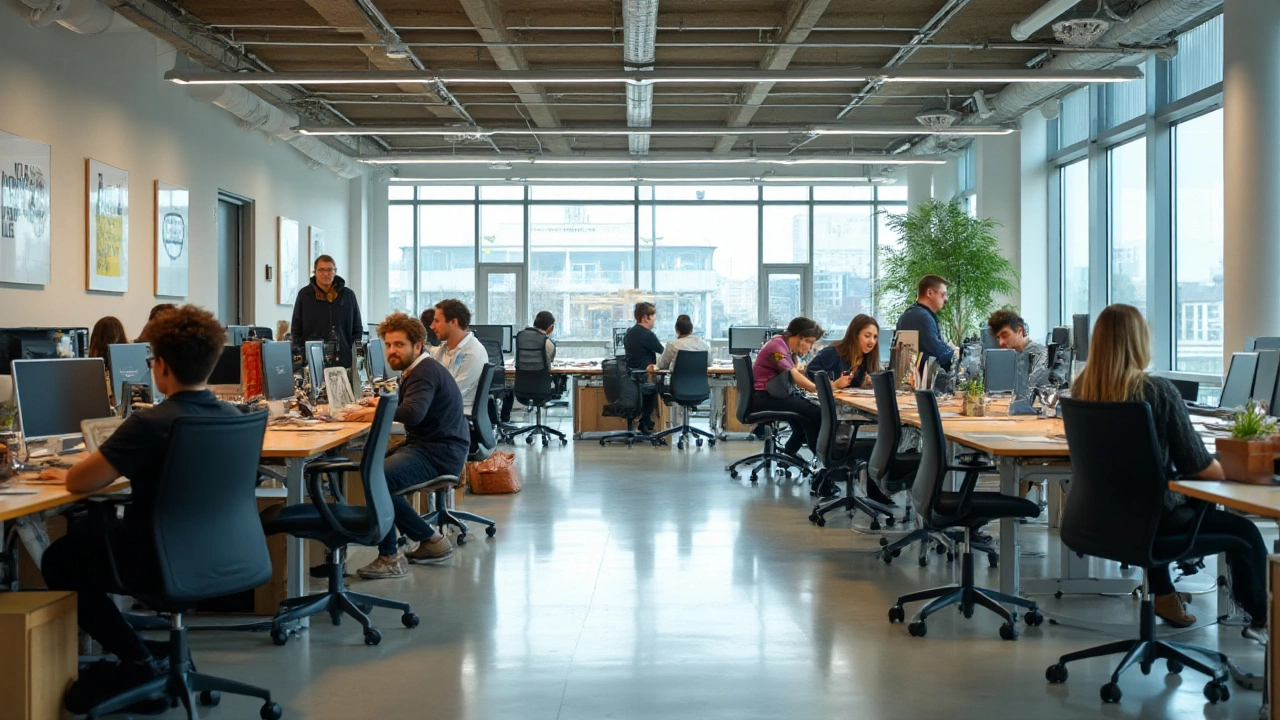
Impacts on Design and Safety
Type C construction plays a pivotal role when it comes to how architects and engineers design commercial buildings. With its emphasis on reduced fire resistance requirements, Type C construction allows for more flexibility in terms of material selection and architectural detailing. However, it doesn't mean that safety is overlooked. In fact, safety measures are still very much a priority, but they are approached differently. For example, in Type C buildings, the focus often shifts to ensuring that evacuation routes are clear, accessible, and easy to navigate in the event of an emergency. Safety planning becomes an exercise in strategic design where architects must balance aesthetics, utility, and compliance with existing building codes. By working within the parameters set by Type C guidelines, designers have more freedom to innovate while still adhering to essential safety protocols.
One of the main impacts of Type C on building design is the selection of materials. Because these structures typically involve less costly fire-resistant materials compared to Type A and B constructions, there can be a notable reduction in building costs. This economic aspect often makes Type C an attractive option for developers looking to maximize budget efficiency without compromising on the functional scope of a structure. It's not just about using cheaper materials, but using materials that meet the necessary safety standards in a cost-effective manner. The materials used in Type C construction, such as wood or lightweight steel, allow architects to experiment with unique architecture styles, offering a diverse range of design possibilities that can cater to specific client needs or geographical considerations.
When examining safety within Type C construction, it's crucial to look at how fire safety regulations are met. These buildings generally feature advanced smoke detection systems and strategically placed sprinkler systems to mitigate risks. Modern Type C designs heavily incorporate materials that, while not as inherently fire-resistant as those used in other classifications, are still compliant with regulations through the addition of protective coatings or treatments. In addition, fire safety features like compartmentation are used to slow down the spread of fire should it occur, demonstrating how safety is cleverly integrated into an ostensibly less secure construction type.
As noted by the National Fire Protection Association, "Integrating smart safety designs and ensuring compliance can yield a safe environment without compromising on design."
Type C construction impacts the regulations surrounding occupancy types and building heights, directly influencing design choices. While these buildings often cater to less densely occupied structures such as warehouses, small retail spaces, or residential buildings with fewer floors, the consideration of design and use is tailored to the building's maximum height restrictions. Strategic planning allows designers to utilize open spaces and versatile room layouts, which can be customized depending on how the building will be used. This approach stands to benefit tenants or businesses that occupy these buildings, offering configurations that serve their operational needs effectively.
Given these various design considerations, it's important to recognize that flexibility is the key benefit of choosing Type C construction. The ability to balance safety with budget and style is a significant advantage provided by this classification. As we move forward in an ever-evolving construction landscape, the adaptability offered by Type C can foster innovative architectural solutions that align with contemporary demands and trends, proving that safety and aesthetics can indeed go hand in hand.