If you asked my seven-year-old Sawyer what the cheapest way to build a house is, he'd probably grab some LEGO and say, "Just stack 'em!" And honestly, he’s not far off. Building cheap isn’t magic—it’s about stacking the right stuff in the right way, skipping things that don’t matter, and not getting tricked by trends. Forget Ferraris and gold-plated sinks. What really matters is getting a roof over your head without wrecking your savings. So, what’s the cheapest way to build? And why is everyone from your neighbor to developers looking for the next affordable building hack?
What Makes a Building Method Cheap?
Alright, let’s start with what actually makes a building method cheap—or not. It’s not just the sticker price on that bundle of lumber, but everything from labor costs, speed of construction, the price of finishes, local building codes, and even how easy it is to find materials in your zip code. Ever heard of cost per square foot? Builders love this number. In June 2025, the national average to build a home in the US hovered around $155 per square foot, but cut that by half in parts of Texas or Mississippi by tweaking materials and designs. Material shortages still make headlines, but alternatives (think new mixes for concrete or recycled steel) keep changing the game.
You also can’t ignore labor. In the US and UK, labor costs eat up about 40% of the budget for most builds. The less specialized the crew you need, the less you’ll pay. That’s why some ultra-simple building methods—like modular or panelized systems—win big on price. Then there’s energy use. Cheaper to build is great, but nobody’s happy if your bills keep climbing. Smart design means less spent both upfront and in the years to come. So when folks talk about the cheapest way to build, you want to look at the full picture, not just what you save at checkout.
Here's something wild: In China, some entire apartment buildings are now being 3D printed for under $50 per square foot in pilot projects. While the tech isn’t quite mainstream everywhere yet, it does show how new ways of thinking bring costs down fast. And sometimes, what counts as “cheap” is just picking what’s local—and skipping complex finishes. Mud, bamboo, even straw bales made a comeback in 2023. If it’s around you and people know how to use it, you’re halfway there.
Budget-Friendly Construction Methods You Can Actually Use
Everyone wants the magic bullet. Spoiler: It’s about combining a few proven methods and being smart about what you skip. Here are some of the most wallet-friendly options actually making a dent in 2025.
- Modular and Prefab Construction: These aren’t your 1950s trailer homes. Modern prefab modules are made in a factory, trucked to your lot, and clicked together like giant building blocks. You can go from concrete slab to livable in weeks, not months. According to the Modular Building Institute, you can save 10-20% on labor and up to 30-50% on time. There's less waste, and weather won't grind your project to a halt.
- Concrete Block (CMU) Construction: Super popular in hurricane-prone states because it stands up to wind and water. CMUs (that’s concrete masonry units for the nerds) are easy to stack, cheap to find almost anywhere, and lower maintenance. According to the National Association of Home Builders, CMU homes can cut long-term maintenance costs by 14% over ten years.
- Earthbag & Rammed Earth: Think walls made by stacking sacks of earth or packing dirt into sturdy forms. These methods need more sweat (often by the homeowner) but almost zero fancy tools. Used everywhere from South America to eco-communities in Arizona, earthbag homes can go up for as little as $50 per square foot if you handle labor.
- Straw Bale Construction: Not just for fairy tales. Straw is cheap, super-insulating (think R-values in the high 30s), and often comes from local farms. A typical straw bale home now costs about 15-25% less to build than a wood-framed house, according to stats from the Natural Building Network.
- Structural Insulated Panels (SIPs): These giant "sandwiches" of foam between two boards make super-fast, strong walls. Expect to cut heating and cooling costs by up to 60%. Upfront, SIPs can cost a bit more per panel, but they save serious cash on labor.
Each of these methods comes with trade-offs. Want fast, mass-produced, predictable? Go prefab. Looking for low bills and crunching your own gravel? Consider earthbag or straw. The cool part is, these aren’t just for hippies—developers are jumping in too. At least a quarter of new housing developments in Oregon last year mixed some prefab panels in to shorten timelines and cut overruns.
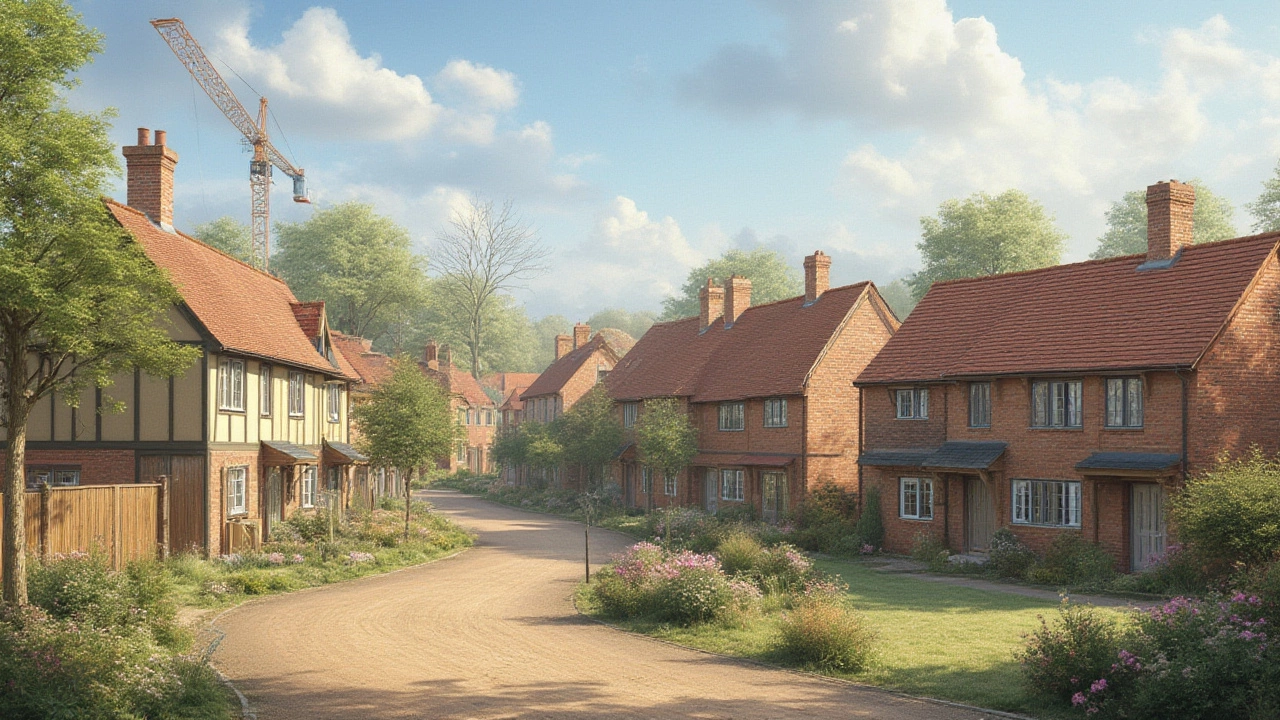
Crunching the Numbers: Actual Costs and Comparisons
Talk is cheap, but hard numbers tease out the real deals. Here’s what you’re looking at (all numbers based on 2025 averages for the US):
Building Method | Estimated Cost per Sq. Ft. | DIY Friendly? | Energy Efficiency | Speed |
---|---|---|---|---|
Prefab/Modular | $80 - $130 | Yes | Good | Very Fast |
CMU/Concrete Block | $90 - $150 | Medium | Great | Medium |
Earthbag Construction | $50 - $85 | Yes* | Excellent | Slow |
Straw Bale | $75 - $125 | Yes* | Excellent | Medium |
SIPs | $120 - $180 | No | Best | Fast |
*DIY friendly, but expect some real elbow grease and learn-as-you-go moments. And a lot of muddy pants (ask Max, my Labrador—he loves ‘helping’ out with our backyard projects).
Notice how low earthbag construction runs? It’s because the main ingredient is dirt—just add sweat. Prefab is sometimes pricier per square foot, but it wins if you're all about speed, tight deadlines, or low labor.
Here’s a fun fact: In 2024, the average DIY earthbag home built by two people over a summer cost under $60,000 for 900 sq. ft.—and that includes passive solar features. Compare that to an entry-level new build at $140,000 for the same size. No fancy finishes, but still surprisingly comfy.
Real-World Tips for Lowering Your Building Costs
Dreaming about cheap construction is one thing. Actually slashing costs takes hustle, creativity, and not being afraid to dig (literally). Here’s what seasoned builders—and stubborn DIYers like me—have learned the hard way:
- Keep it Simple: The cheapest houses to build are simple boxes. Every bump, bay, or curve ups your labor and material costs fast. That Instagram-worthy turret? Kiss $20k goodbye.
- Use What’s Local: Hauling stone or timber across the country drains your budget. Local sawmills, reclaimed bricks, or even urbanite (recycled sidewalk concrete) can mean huge savings. Look for salvage yards and demolition sales if you’re flexible about finishes.
- Go Small, Think Efficient: Smaller houses aren’t just cheaper in materials—they’re faster to heat, cool, and fix. Studies in 2025 saw more Americans building homes under 1,200 sq. ft. than at any point in the last decade. If you add storage-smart designs and good insulation, it feels way bigger inside.
- Partner Up: Community builds or group buys on materials drop costs. Some folks even trade labor days on projects—help your neighbor pour a slab, they help with your roof. I once swapped two full days helping my buddy install drywall for him framing an interior wall with me—cheapest labor I ever bought.
- Be Ready to Sweat: The more work you do yourself, the more you save. But be real about your limits—some things (like electrical and plumbing) need pros for safety and code. Still, painting, landscaping, and simple framing or siding? Very DIY-friendly.
Try this too: Before you commit, get three bids for each part of your build. Prices can swing wildly for the same job, depending who’s in demand. And if you hear “I can start next week,” don’t be afraid to negotiate.
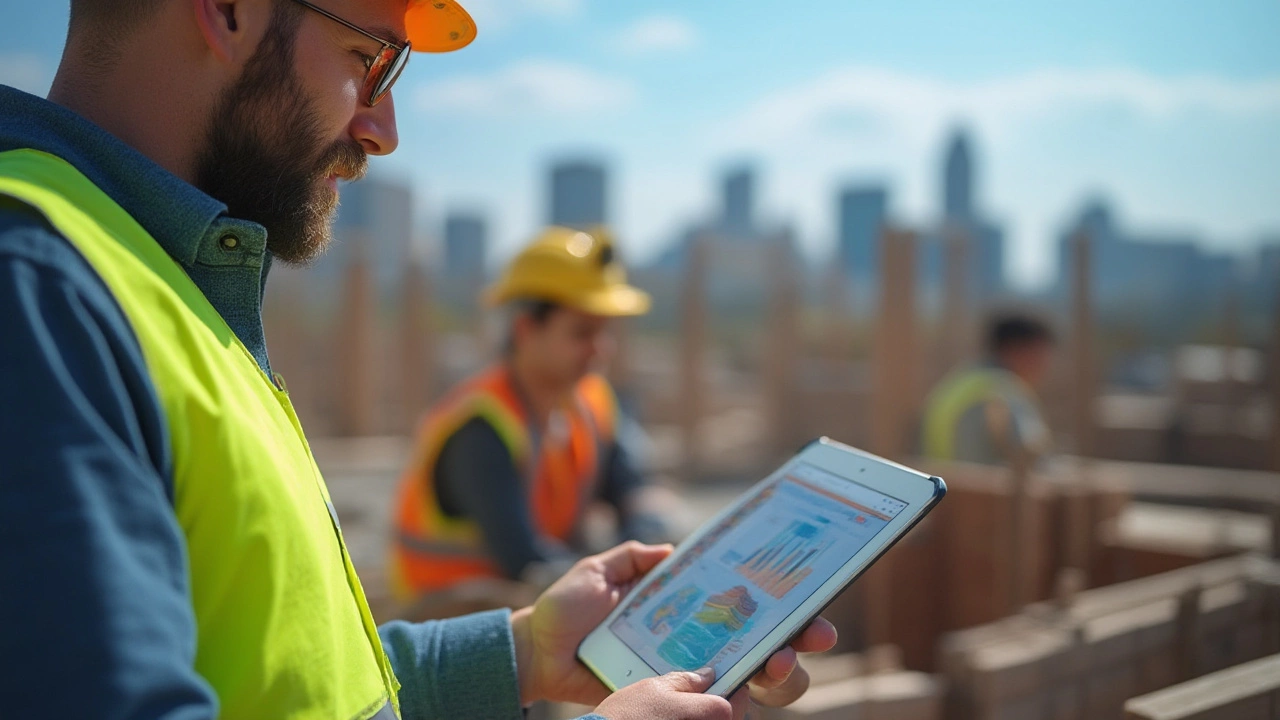
Cheap Doesn’t Mean Bad: Balancing Savings and a Good Home
Some folks hear “cheap” and think “falling apart” or “ugly.” That’s just not true. Cheap building is about smart choices, not cutting corners. Plenty of ancient buildings—think 800-year-old rammed earth homes in Europe or timber cabins in Canada—were built using the same dirt-simple methods folks are re-discovering now. Turns out, they’re still standing.
It’s worth weighing long-term durability against upfront budget. For example: A steel roof might cost a few grand more at first, but lasts 3x longer than shingles—saving thousands in the next 20+ years. That’s why some ultra-budget builds spend extra on roof and foundation, using cheaper methods for walls and finish.
And don’t forget life in the house. Good design (big windows, smart insulation, shaded porches) means lower bills and a more comfortable space. In hot states, even the cheapest homes can stay cool if you orient the windows right or use earth berms.
If you’re building in 2025, new tech means you’ve got more choices than ever. But the fundamentals of cheap building stay the same. Stack simple shapes, use what’s close, don’t pay extra for style that doesn’t buy you comfort or safety. Trust your instincts—and if you don’t have them yet, borrow a neighbor’s. Or just ask your kid. Sawyer says, "If you mess up, you can always build it again. That’s what Dad does." And he’s not wrong.
Building cheap isn’t about being cheap—it’s about being resourceful. If you get creative, stay open-minded, and aren’t afraid of a little dirt under your nails, you’ll be surprised what kind of sturdy, comfortable, and affordable home you can call your own.