Have you ever thought about building your own home and wondered why it's so expensive? You're not alone. Costs are up, and everyone's feeling the pinch.
First off, materials costs. Remember how it seemed like plywood and concrete prices were skyrocketing? Well, that's because they were. Supply chain hiccups, factory shutdowns, and increased demand for home improvement projects have all driven material prices through the roof.
Couple that with a labor market that's tighter than a pickle jar lid. Skilled workers are in high demand but short supply, which means higher wages and more competition to snag good help.
- Material Costs and Shortages
- Labor Market Challenges
- Permits and Regulations
- Location and Land Prices
- Design Complexity and Custom Features
- Tips for Cost-effective Building
Material Costs and Shortages
Alright, let's dive into the nitty-gritty of why building a house costs what it does with a focus on material costs. Over the past few years, prices for construction materials like lumber, steel, and concrete have surged. What's going on?
Supply Chain Woes
First, supply chains aren't exactly firing on all cylinders. Ever since the pandemic hit, factories have been playing catch-up, and it's still a bumpy road. Shipping delays and port congestion add to the drama, making it tough for builders to get what they need when they need it.
Demand Outweighing Supply
Next up is the good 'ol supply and demand. During the lockdowns, folks went nuts on home improvements. More demand but the same old supply? You guessed it, prices shot up. Add to that the rise in new builds as more people are looking to personalize their spaces.
The National Association of Home Builders reports, "Lumber prices surged more than 50% in 2023, contributing significantly to increased costs for new construction."
Impact on Building Costs
Here comes the kicker: all these increased costs translate directly to your new home's price tag. Higher material costs mean builders are spending more, and believe me, those expenses get passed down to the buyer.
What You Can Do
- Shop around for local suppliers who might offer lower rates.
- Consider alternative materials that are less affected by shortages.
- Be flexible with your timeline—some costs might drop if you're not in a rush.
So, while the dream of a brand new build might be costly, understanding these factors can help bring some relief and maybe even a strategy to tackle these obstacles.
Labor Market Challenges
Building a house isn't just about bricks and mortar; it's also about the labor working tirelessly to realize those architectural dreams. And let's face it, the labor market lately has been having a bit of a crisis.
One of the main issues is the shortage of skilled workers. Over the last few years, fewer people have been joining the trades, leaving a gap in the workforce that new builds desperately need to fill. With fewer hands on deck, projects take longer and cost more. This isn't just a local problem; it's happening on a global scale.
The Vanishing Workforce
But why fewer workers? Well, younger generations are often steered toward college degrees, leaving fewer apprenticeships being filled in fields like carpentry and plumbing. The generational shift means industries have to work harder to attract and retain talent. According to a report from the National Home Builders Association, more than 80% of builders cited labor shortages as a significant problem, affecting timelines and budgets.
“The skilled labor shortage is arguably the most acute problem the housing sector faces today,” said Robert Dietz, Chief Economist at the National Association of Home Builders.
Impact on Construction Costs
What does this mean for your new home build? For starters, it can increase overall construction expenses. With fewer workers available, those in the business can command higher wages, a cost that builders pass on to you, the homeowner. It's a bit of a domino effect: fewer workers mean higher wages, which means higher overall costs.
Additionally, expect delays. A project that could have taken six months in the past might stretch to eight or even ten months today. It's important to plan for these delays in your budget and timeline to avoid stress down the road.
Steps Toward a Solution
- Consider looking into smaller, local builders who might have more availability.
- Plan your build in the off-season when the demand for labor isn’t as high.
- Explore modular homes or prefab options, which can reduce on-site labor needs.
By understanding these labor market challenges, you can better prepare for the hurdles and hopefully, manage your expectations and budget more efficiently.
Permits and Regulations
Alright, so let's talk about the bureaucratic side of things. Ever think about why you need permits just to build on your own land? It boils down to making sure everything's safe and up to code. Cities and towns have rules to ensure buildings can withstand the elements and won't cause neighborhood headaches.
When you're diving into new builds, permits are non-negotiable. They cover everything from zoning laws to environmental regulations. You might need separate permits for plumbing, electrical work, and of course, the granddaddy of them all, the building permit itself.
Why You Need Them
These permits protect you. Imagine building your house only to find out later it doesn’t comply with local codes – you'd be facing hefty fines or even being told to tear it down. Ouch, right? The costs and time involved in getting permits can be a drag, but consider them insurance against future headaches.
How to Navigate Permit Maze
- Research what permits you need based on your location.
- Visit your local building department early on to get a list of requirements.
- Consider hiring an expert, like an architect, to guide you through this maze.
- Give yourself time; approvals aren’t instantaneous and can take weeks or even months.
Type of Permit | Average Cost | Typical Approval Time |
---|---|---|
Building Permit | $1,200 - $2,000 | 2-3 weeks |
Electrical Permit | $150 - $500 | 1-2 weeks |
Plumbing Permit | $100 - $400 | 1-2 weeks |
Knowing what permits are required and how long they take can save you a boatload of stress. It might be one of the more mundane aspects of building, but understanding construction expenses related to permits is key to getting your dream home off the ground without a hitch.
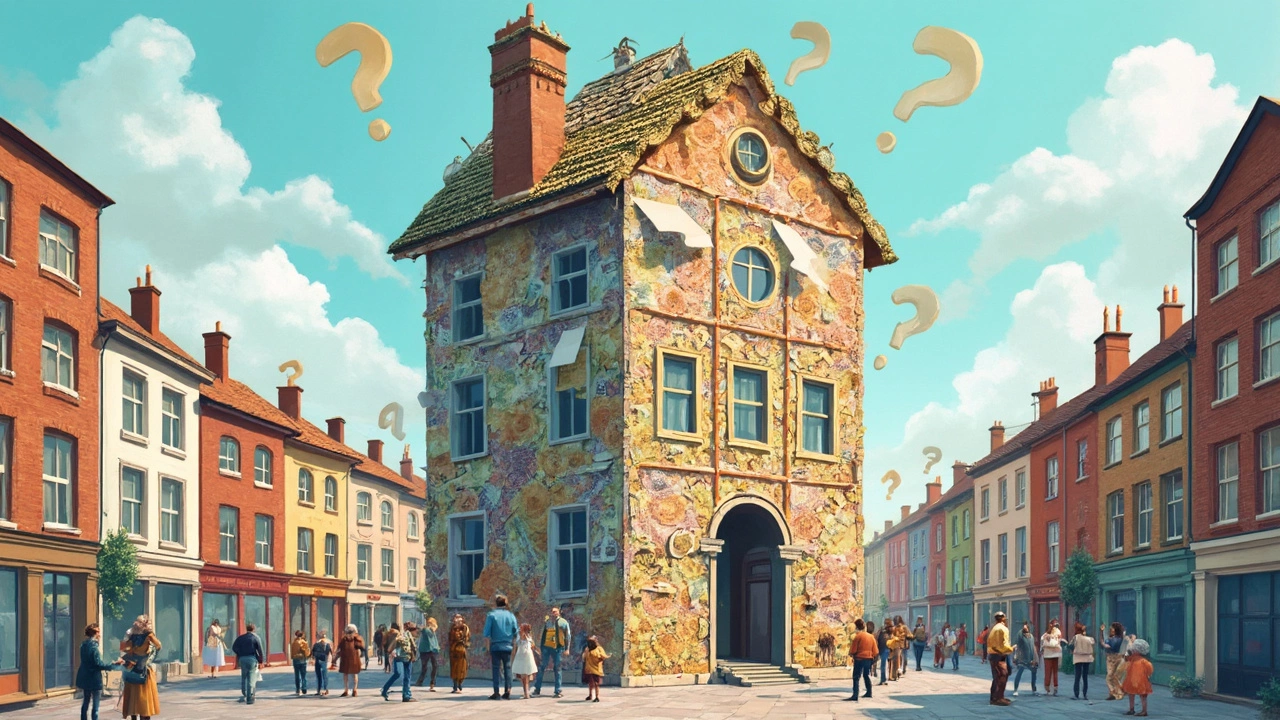
Location and Land Prices
When it comes to the cost of building a house, location plays a massive role. Imagine wanting to build in a bustling city like San Francisco versus a small town in Nebraska—your wallet's gonna feel the difference!
Let’s dig into why. Urban areas usually come with a hefty price tag for land, simply because everybody wants a piece of the action. More people, more demand, higher land prices. It’s basic economics.
Land prices can vary due to several factors including the proximity to amenities, schools, public services, and even public transportation. For instance, a plot close to a good school will likely set you back more than one that’s a bit out in the boonies.
Mark Fleming, chief economist at First American Financial Corporation, noted, "Location is not just about geography. It’s an expression of demand reflecting the value of being close to services, stores, and other essentials."
A lot of folks are also facing issues with zoning laws and regulations, which can add hidden extra costs. Urban areas especially may have stricter zoning that requires specific steps to be followed before building can even start. Cha-ching, more money down the drain!
Understanding Regional Trends
There's also this interesting shift happening. Remote work is pushing people out of the big cities and into the suburbia or beyond, which is starting to inflate land costs in traditionally cheaper areas. It's like a domino effect, changing the housing cost landscape.
Location | Average Land Price (per acre) |
---|---|
San Francisco, CA | $1,200,000 |
Omaha, NE | $60,000 |
Austin, TX | $300,000 |
So, how do you make a smart move with such high land prices? Consider looking a bit further out than the hot spots. Sometimes going just a few miles away from the city can save you a bundle, and in today’s work-from-home culture, it might not make a big difference.
Design Complexity and Custom Features
When it comes to building a new home, design complexity can be like adding a few extra scoops of ice cream to your order—it might seem like a good idea, but it also comes with a bigger bill. More custom features and intricate designs require specialized labor and extra time, which means more money out of your pocket.
Let's start with architecture. You might think having a unique, standout design is essential, but complex designs often need specialized architects and engineers, which ramps up fees. Every curve, unique angle, and modern feature adds layers of planning and construction challenges.
Impact of Customization
Opting for custom features like gourmet kitchens, luxury bathrooms, or even smart home tech can strain your budget. These aren't just about the cost of materials but also the skilled labor required for installation. Construction expenses skyrocket when you go for those state-of-the-art, fully wired, smart home that connects your thermostat to your fridge.
Modern Trends
Current trends like open floor plans and eco-friendly materials also come into play. While they look great and may save energy bills in the long run, the initial investment is hefty.
Cost Comparison
Have a peek at how custom features can vary:
Feature | Standard Cost | Custom Cost |
---|---|---|
Kitchen | $20,000 | $50,000+ |
Bathroom | $10,000 | $25,000+ |
Smart Home Setup | $5,000 | $15,000+ |
These figures underscore the stark difference and can help when you prioritize your must-haves.
Keep It Simple (Sometimes)
If you're looking to cut costs, consider simplicity in design. Streamlined designs often offer aesthetic charm without all the extras. So, while that spiral staircase might look cool in glossy magazines, a classic, straight staircase is typically more budget-friendly.
Understanding how house cost aligns with your design choices can help avoid budget surprises. Whether you're yearning for that custom wine cellar or floor-to-ceiling windows, plan accordingly and make informed decisions to keep your dream home from becoming a financial nightmare.
Tips for Cost-effective Building
Building a house without breaking the bank is a top goal for many, but where do you even start? Here’s how you can take those construction expenses down a notch:
1. Choose the Right Timing
Building during off-peak times can sometimes lower costs. Contractors aren’t as busy, meaning better availability and potentially better prices. But remember, weather conditions are essential, so don’t compromise on that just to save a few bucks.
2. Simplify the Design
Fancy designs can run up the price. Think about minimizing unnecessary corners or unique building shapes. Staying practical in the design phase keeps costs predictable.
3. Source Local Materials
Local materials not only support the community but cut down on shipping costs. Just make sure you’ve done your homework on the quality to avoid any costly repairs down the line.
4. DIY Where Possible
This might sound ambitious, but pitching in on simple tasks can help. Painting, landscaping, or even basic carpentry for those who’ve got the knack—every bit helps keep that budget steady.
5. Get Multiple Quotes
Don’t settle for the first contractor or supplier. Get at least three quotes to see the price spectrum and ensure you aren't overpaying.
6. Monitor Your Budget Closely
Any successful budget needs careful management. Track everything from house costs to unexpected expenses. It's easier to adjust on the go than dig out of a hole later.
Strategy | Possible Savings |
---|---|
Off-Peak Building | 5-10% |
Simple Design | 15-20% |
Local Materials | 5-10% |
DIY Tasks | Variable |
Competitive Quotes | 5-15% |