Picture any city skyline—towering buildings, busy commercial centers, cozy houses. None of this comes out of thin air. We build with matter pulled from the earth, transformed in factories, mixed with innovation, and carried onto muddy job sites. And here’s a crazy stat: the worldwide construction sector gobbles up about 40% of all raw materials extracted each year. Not only is that a mind-boggling amount, it tells you how massively important these materials are for, literally, everything around us.
Core Raw Materials: What Every Building Needs
If you’ve ever looked at a construction site and wondered what’s actually going into the bones of that new house or apartment block, here’s the real stuff. At the base of most structures are some familiar names: sand, gravel, stone, cement, bricks, steel, and timber. These aren’t just tradition—they’re the tried and tested basics that keep buildings standing tall.
Sand might sound almost boring, but it’s the humble hero behind both concrete and mortar. Believe it or not, the world uses so much construction-grade sand, it’s running short in some places! Regular beach or desert sand isn’t good enough—builders need the angular kind found in quarries and riverbeds, which holds concrete together better.
Now, toss gravel and crushed stone into the mix, and you’ve got "aggregate." Concrete calls for a specific blend, mixed with water and cement, until it becomes the gray stuff we all know. Cement—the powdery binder in the trio—is made from limestone, clay, and a sprinkle of gypsum. When you mix cement with water, it reactions and hardens, turning into the glue that holds bricks and rocks together.
Speaking of bricks, these little rectangles can be made from clay, shale, fly ash, or even concrete. Fired at high temperatures, clay bricks become weatherproof and tough—ideal for walls and facades. Meanwhile, concrete blocks are heavier hitters, perfect for the structural grid of skyscrapers and warehouses.
Then there's steel. Huge skyscrapers? Bridges? Factories? Steel’s your workhorse. Iron ore, coal, and limestone get cooked up in blast furnaces, then shaped into rods, beams, and rebar. One cool fact: rebar (those ribbed steel bars you see poking out of foundations) gives concrete its remarkable strength against bending and stretching.
Wood’s another must-have, especially for detached homes and low-rise buildings. It comes in species like pine, spruce, fir, and oak. Sustainable forestry matters big time—there’s growing demand for certifiably green lumber, tracked from seedling to finished beam.
Material | Global Use (Million Tons) | Primary Use |
---|---|---|
Sand/Aggregate | 40,000 | Concrete, Roads |
Cement | 4,500 | Concrete, Mortar |
Steel | 2,000 | Structures, Reinforcement |
Timber | 1,800 | Framing, Finishes |
Bricks/Blocks | 1,500 | Walls, Partitions |
It's nuts just how much of this stuff the world uses every year. If every person carried their 'fair share' of construction materials, it’d be more than their own body weight, every single year. And since the construction industry keeps growing, so does demand for these heavy hitters.
New and Evolving Materials: Sustainability and Innovation
The classics—sand, cement, steel, wood—aren’t the only show in town. More and more, construction companies are getting creative, looking for alternative or more sustainable raw materials. You might be surprised at what counts as a building block in 2025.
First up: recycled aggregates. Every year, mountains of old concrete and bricks get torn down. Crushing and re-using these for new building projects keeps rubble out of landfills. Builders have figured out how to mix in recycled aggregate without sacrificing the quality or strength of modern concrete.
Bamboo is making waves, especially in Asia and South America. Tougher than most people expect, bamboo grows fast and soaks up carbon from the atmosphere. With proper treatment to protect against bugs and rot, it makes for strong scaffolding and even structural beams.
Then you’ve got engineered wood products—things like cross-laminated timber (CLT) and glulam beams. These are made by gluing and pressing together layers of wood. Amazingly, tall buildings up to 18 stories are now being built with these wood composites, thanks to their high strength-to-weight ratio.
All this effort isn’t just for bragging rights. The construction sector generates around 39% of the world's carbon emissions when you factor in energy use and material production. So swapping in "greener" materials can make a huge difference to a project's environmental footprint.
Some companies are tinkering with hempcrete (hemp fibers mixed with lime for insulation), straw bales as natural walls, and even plastic waste for bricks. While these aren't mainstream yet, they’ve become the talk at green building expos. Tips for choosing sustainable materials? Look for third-party certifications (like FSC for wood), ask about recycled content, and don’t be afraid to push for locally sourced materials to cut transportation emissions.
What about the basics like glass, insulation, and paint? There’s plenty happening there too. "Low-E" coated glass keeps buildings cool by blocking infrared rays, while mineral wool and cellulose—made from recycled paper—are outpacing classic polystyrene foam as eco-friendly insulators.
Bottom line: the toolkit for modern construction has never been wider or more exciting. If you’re planning a building project, there’s a wider menu of raw materials than ever before, each with its own upsides. Check for suppliers who invest in sustainable and responsibly sourced products—it pays off in lasting quality and public trust.
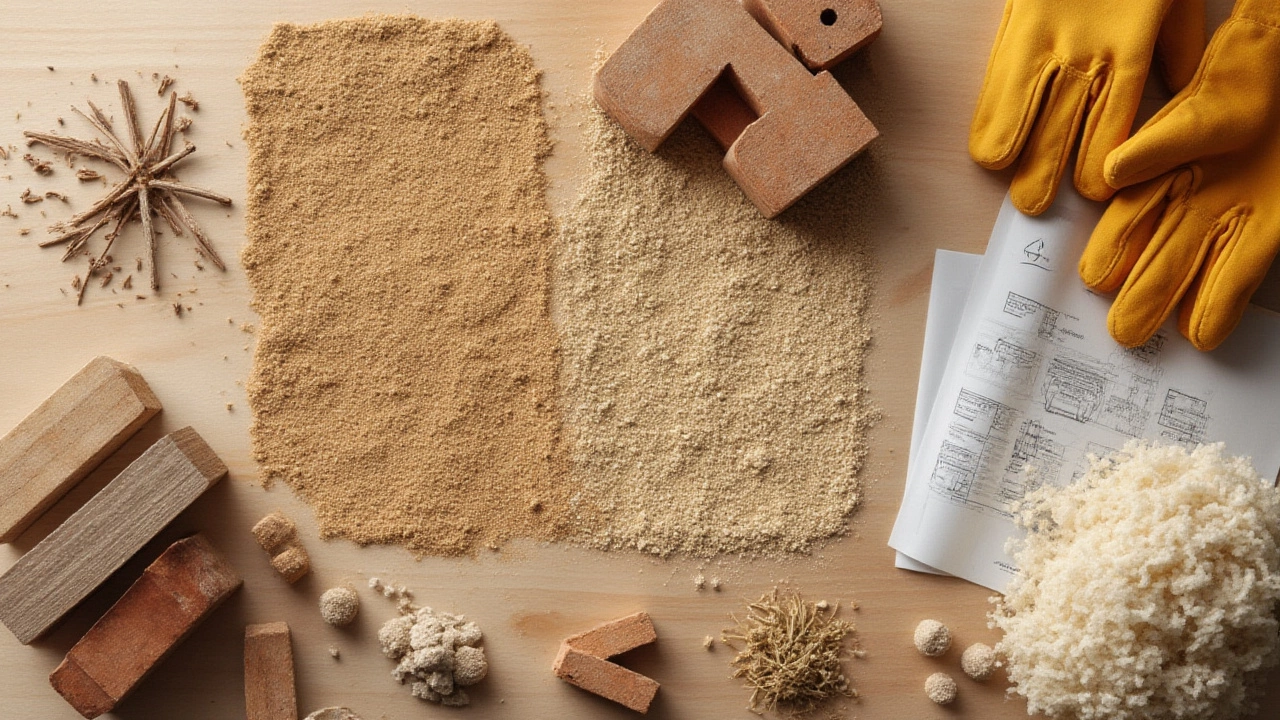
How Material Selection Impacts Every Construction Project
You can’t just throw any material at a wall and call it a day—what you choose changes everything. Builders, architects, and project managers have to think about loads (how much stuff the building will carry), weather, cost, and deadlines. The real world is never ideal, so every material pick comes with trade-offs.
Heavier materials like concrete and steel work best for skyscrapers, bridges, and parking garages. They handle massive loads, high winds, and keep fire risk low. But heavy materials mean hefty transportation bills—and in remote locations, it’s a logistics puzzle. On the flip side, timber and lightweight steel fit the bill for homes and smaller office blocks. They go up fast and don’t need ultra-strong foundations.
Another tip: climate plays a huge role. In places with tons of wind and rain, brick and stone cladding holds up better than wood siding. In earthquake zones like California or Japan, reinforced concrete or steel framing is a must—flexibility and strength matter more than anything.
There’s cash to consider, too. Steel prices shot up by nearly 60% in some markets during 2024, rattling project budgets. Builders started pivoting to composite materials or recycled metals to keep costs from spiraling out of control. Sand is another wild card—legal and illegal sand mining caused bottlenecks, so sourcing from trusted, ethical suppliers is a growing headache for project managers.
Want your building to last? Pick materials that resist moisture, rot, and insects. Modern pressure-treated lumber, coated steel, and engineered woods push service lifetimes way past what natural, untreated stuff managed in the past. If speed matters—like rebuilding after a storm—modular materials (precast concrete panels, structural insulated panels) slash build times by weeks or months.
A cool example: the world’s first "carbon-neutral" office tower in Norway used a combo of CLT, recycled steel, and locally quarried stone, cutting total construction emissions by about 60%. They even composted leftover wood scraps to fertilize local parks! Good material choices don’t just help the planet—they often save you cash and headaches long term.
Here’s one takeaway: be flexible. Builders who adapt to market conditions, changing laws, and new supply chain wrinkles stay ahead. If a material shortage hits, having a Plan B—alternative sources or backup materials—keeps your project moving forward.
Key Tips for Sourcing and Managing Construction Materials
Knowing your raw materials is half the battle—the rest is lining up the best deals without sacrificing quality or falling behind schedule. Getting this right is what separates smooth builds from headaches and lawsuits.
First, build relationships with multiple suppliers. If you always go to the same vendor, you’re vulnerable to price swings, shipping delays, or sudden shortages. Top project managers in construction keep 2–3 reliable sources for critical items like aggregate, cement, and steel. If one drops the ball, the others step in.
Second, watch for certifications and track records. Whether it’s concrete, wood, or stone, ask to see test reports, safety data, and production certifications. For big projects, some regions make these documents mandatory. Spot-checking helps prevent illegal logging, unsafe working conditions, or poor-quality product sneaking in.
Third, time your material purchases. Cement can’t sit around forever, and steel beams rust if left in the rain. Smart scheduling—"just in time" delivery—cuts waste and theft. For projects using imported materials, factor in customs, fuel prices, and seasonal slowdowns. Did you know container shipping costs tripled in 2021? Those prices haven’t dropped much, so watch your bottom line.
Fourth, stay tech-savvy. There’s software now that tracks your stockpiles, orders automatically, and gives alerts if delivery is overdue or a batch fails inspection. On a 2024 highway project in Texas, these digital tools helped reduce material over-ordering by 25%, saving hundreds of thousands of dollars.
Fifth, think local when you can. Locally quarried stone, native timber, or regional gravel can be cheaper, easier to manage, and make for a project locals want to support. Plus, local materials often mean fewer greenhouse emissions from transport—a bonus in today’s eco-aware world.
Finally, don’t overlook training for your crew. If your workers handle new materials like CLT, hempcrete, or high-tech composites without the right know-how, mistakes might cost a fortune. Bring in experts or send the team for quick training sessions with your supplier.
Remember, every bit of money you save on raw materials—without cutting corners—goes right back into your project’s success. Stay sharp, check your sources, and keep an eye on market shifts. Whether you’re building a backyard studio or the next city tower, the raw materials you choose set the whole tone. The best builders know their stuff inside and out—and never stop learning the ropes, even when a project seems straightforward at first glance.