Type 5 building construction—ever heard of it? If you're in the construction industry or dabble in real estate, you probably have. It's essentially the backbone of many small commercial projects. This is the go-to for many due to its simplicity and cost-effectiveness. Imagine an entire framework mostly made of wood; that's Type 5 in a nutshell.
Why wood, you ask? Well, it's affordable, easy to work with, and if done right, pretty durable. Plus, it offers a degree of flexibility in design that more rigid materials just don't. Not to mention, wood's sustainability factor plays well in today's eco-conscious world. But as with every method, there are challenges too. Fire safety, for example, is a key concern, given wood's natural flammability.
Still, when managed properly with the right treatments and techniques, Type 5 constructions can hold their own pretty well when it comes to safety standards. To make the most of this type, understanding the balance between cost, safety, and design flexibility is crucial. Stick around as we unpack what makes Type 5 construction tick and how it could fit into your next commercial project.
- Introduction to Type 5 Construction
- Materials and Techniques
- Pros and Cons
- Safety Considerations
- Applications in Commercial Settings
- Tips for Effective Type 5 Construction
Introduction to Type 5 Construction
Type 5 construction is all about using wood framing. This method is the simplest and usually the most cost-effective when it comes to building smaller commercial spaces. It's popular for those aiming for a quick build without breaking the bank.
Picture a standard residential home. Chances are, it's a Type 5 structure. But don't think that this approach is limited to residentials. Many small office buildings, strip malls, and even restaurants go this route thanks to its flexibility and affordability.
Wood isn't just used for wall frames; you’ll find it in floors and roofs too. The idea here is to keep things straightforward. Wood offers a level of customization that other materials can't match. Need an open floor plan? Type 5’s got you covered.
Why Choose Type 5?
So, why would someone pick Type 5 construction over other types? The big reasons are cost and speed. Wood is easier on the wallet compared to steel or concrete, which makes it attractive for developers and investors. And if you’re in a hurry, wood can significantly speed up the building process, often cutting months off the timeline.
Plus, if eco-friendliness is a concern, wood has a smaller carbon footprint than more industrial alternatives. It’s a renewable resource, too, which scores it points in the sustainability department.
Considerations and Challenges
But before you make up your mind, consider a couple of challenges. Type 5 construction is less robust when it comes to fire resistance. Wood burns, after all. However, with modern fire-retardant treatments and building codes, this is less of a dealbreaker than it used to be.
Moisture can also be an issue. Wood absorbs water, which can lead to long-term problems like mold or weakening of the structure. This is why a solid understanding of proper sealing and water management is essential.
Ultimately, Type 5 construction offers a mix of benefits and challenges. Knowing when and where to use this construction type can make all the difference in the outcome of your project.
Materials and Techniques
When it comes to Type 5 construction, the main material hitting the spotlight is wood. It's not just any wood though; we're talking about heavy-duty, ready-for-action types like plywood, oriented strand board (OSB), and dimensional lumber. These materials form the crux of the wood framing method, often making up walls, floors, and even the roofs in these buildings.
If we dive into framing techniques, the two most common are platform and balloon framing. Platform framing is like building a house layer by layer, with each floor serving as a platform for the next. It's popular because it allows workers to build one level at a time, which is super manageable and kind of a no-brainer for multi-story buildings.
Key Techniques
Platform Framing: Each floor is built individually, creating a 'platform' for the next. It's safer and more straightforward. The weight distribution is pretty even, which keeps things stable.
Balloon Framing: Less common these days, but it's a technique where long, vertical boards run from the foundation all the way to the roof. Used often before platform framing became the norm, it's still seen in some historic buildings.
Safety and Efficiency
Despite the somewhat combustible nature of wood, Type 5 construction employs techniques like fire-resistant coatings to beef up safety. Also, the use of advanced joint and bracing methods ensures stability, making these buildings not just light on the pocket but also robust and safe.
Apart from wood, you might spot other materials enhancing the core structure. For instance, steel plates and fasteners often play a role in holding wood members together, creating a strong yet flexible structure.
Material | Use | Properties |
---|---|---|
Dimensional Lumber | Framing | Strong, versatile |
Plywood/OSB | Flooring, walls | Stable, resistant to bending |
Steel Fasteners | Joints | Tensile strength, non-corrosive |
Using these materials and techniques optimally requires precise planning and coordination. It’s crucial to align with local building codes and consider factors like insulation, thermal performance, and weather resistance, depending on the project's locale. For those venturing into commercial construction, knowing these basics helps tailor the building process to your specific needs.
Pros and Cons
Thinking about jumping into Type 5 construction? Let's break down the good and the not-so-good in simple terms.
Pros
Flexibility is the name of the game with Type 5 projects. The use of wood allows for design tweaks and changes without busting your budget. Need an extra window or a last-minute wall shift? No problem!
Speaking of budget, cost-effectiveness is a major plus. Wood is generally cheaper and more accessible. Plus, labor costs might be lower since many contractors are familiar with wood framing techniques. Whether it's a small retail space or an office, Type 5 can offer a financially savvy solution.
And let's not forget sustainability. Wood is a renewable material, and more suppliers these days are providing sustainably sourced options. This is great for those looking to reduce their ecological footprint or gain some green building creds.
Cons
With all the good stuff, there are a few trade-offs. The first one? Fire safety. It should not come as a surprise that wood burns. While modern treatments and methods improve safety, you still need to be cautious and often adhere to stricter fire codes.
Then there's the durability factor. While flexible, wood isn’t always the best for longevity, especially in harsh weather environments. Moisture can be a real threat, leading to issues like rot or mold if not properly managed.
Finally, consider insurance costs. Because of the safety risks, especially fire, insurance premiums for Type 5 buildings can be higher.
Pros | Cons |
---|---|
Cheaper material & labor costs | Higher fire risk |
Flexibility in design | Potential moisture issues |
Sustainable material | Possibly higher insurance costs |
So, what's the takeaway? If you're after a cost-effective and eco-friendly option, Type 5 construction could be perfect. Just keep an eye on fire safety and durability factors to make sure your build goes off without a hitch.
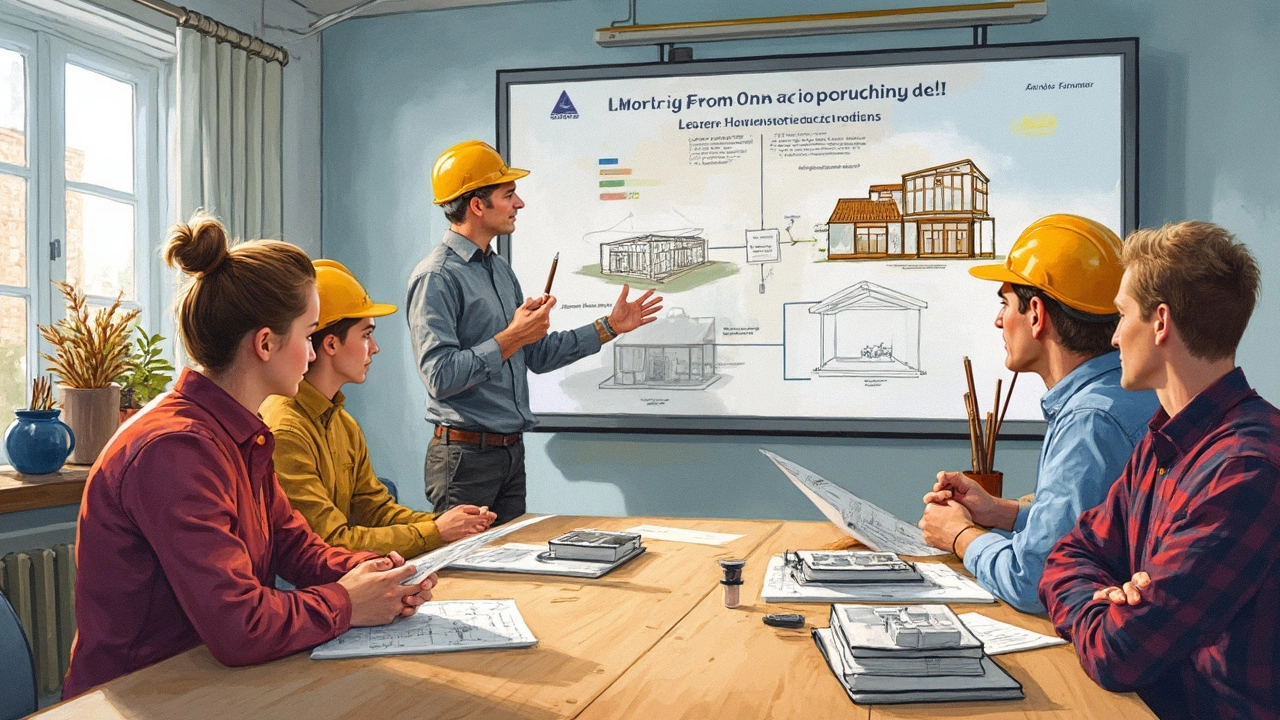
Safety Considerations
When it comes to Type 5 construction, safety is a big deal, mainly because wood is the primary material. It's great for many things, but being fireproof isn’t one of them. So, what's the deal with keeping things safe? Let’s break it down.
Fire Safety Measures
First off, fire prevention is key. Using fire-retardant treatments on wood is one of the best ways to reduce risk. And don't forget about fire-resistant barriers; gypsum boards often do the trick. They help slow down the spread of fire from one area to another.
Then there’s the matter of sprinklers. Installing a modern sprinkler system isn't just an option—it's a must. In many jurisdictions, commercial buildings, especially those using wood, must have them to meet building codes.
Structural Integrity
Ensuring structural integrity during extreme weather conditions is also crucial. Wood can handle a fair bit, but it's not invincible. Using proper bracing and anchoring techniques will go a long way in preventing issues due to wind or seismic activities.
Regular Inspections
How often do you check your smoke alarms? If you're responsible for a commercial site, regular checks and maintenance shouldn’t be overlooked. Scheduled inspections can catch small issues before they become big problems. It's about being proactive rather than reactive.
Training and Awareness
It’s not just about the building materials—human factors matter too. Conducting regular fire drills and safety training sessions can prepare occupants to act swiftly and calmly during an emergency. It's good practice for everyone to know where the exits are.
Design and Planning
During the planning stage of your commercial construction project, consider these safety aspects. Good design can integrate safety measures from the get-go, making the whole process smoother and more effective in the long run.
For a fun fact, did you know that the effectiveness of fire-retardant-treated wood can be enhanced by up to 20% with the proper application techniques? Yep, those details really matter!
Applications in Commercial Settings
When it comes to commercial settings, Type 5 construction often finds its home in smaller projects like retail outlets, boutique offices, and even cozy cafes. The charm of these buildings lies in their adaptability and the cost savings they offer. Plus, they can often fast-track construction time thanks to the simpler techniques involved.
Retail Spaces are a perfect fit for Type 5 construction. Whether it's a chic boutique or a neighborhood grocery store, wood framing allows for versatility in layout and design. It helps businesses customize interiors without a hefty price tag. The focus here is on aesthetics and functionality, which wood delivers beautifully.
Another major application is in restaurant builds. Many cafes and small eateries lean towards Type 5 construction because it offers a warm, inviting atmosphere critical for customer-centric businesses. The wooden frames and exposed beams often become style features, turning structural elements into decorative ones.
Office Buildings
Small office structures also benefit significantly due to the flexibility Type 5 construction offers. Companies looking for modern, eco-friendly spaces love the sustainable aspect of using wood. The charm of an open-plan office with hardwood floors can be quite an attraction in the current market.
Apart from these, Type 5 construction extends its utility to community centers, small clinics, and educational settings like daycare facilities. Wood's ability to absorb sound can be a welcomed feature in busy commercial spaces. Plus, it's no secret that wooden environments can enhance mental well-being, making them ideal for spaces needing a human-friendly touch.
One thing to keep an eye on is the local building codes, which can vary quite a bit. Always make sure the desired construction meets the required safety standards, especially considering wood's different behavior in fire scenarios. Overall, if you're aiming for projects that combine both style and cost-effectiveness without compromising on quality, Type 5 construction holds a lot of promise.
Tips for Effective Type 5 Construction
Getting the most out of Type 5 construction means knowing a few tricks of the trade. Maximizing this method's potential requires balancing cost, safety, and longevity. Let's dive into some practical tips.
Choose the Right Materials
The backbone of Type 5 is, of course, wood. But not all wood is created equal. Opt for high-quality, treated lumber. Treated wood boosts durability and fire resistance, offering a little extra peace of mind.
Focus on Design Efficiency
Fancy designs are nice, but efficiency matters more in commercial construction. Aim for layouts that maximize space without adding complexity. Simpler designs can reduce both construction time and costs, leaving more room for potential profit.
Prioritize Safety Measures
Fire safety is a concern with Type 5, but it doesn’t have to be a deal breaker. Invest in fire-resistant coatings and ensure proper spacing to slow down potential flames. Smoke alarms and sprinklers should be non-negotiables, no matter the size of the project.
Adopt Proper Construction Techniques
Following best practices during construction can’t be stressed enough. Make sure your team sticks to the blueprints and doesn’t cut corners. Attention to detail in framing and spacing will go a long way in maintaining structural integrity and meeting safety codes.
Stay Updated with Local Codes
Building codes vary greatly by locale, especially with materials like wood. Keep yourself informed of any changes or updates to ensure compliance. It’s not just about avoiding fines; it's about maintaining safety for those who'll use the space.
Leverage Technology
Modern construction tech such as 3D modeling software can aid in visualizing and planning projects. These tools can help identify potential problem areas before the build even starts. It'll save you time and likely some headaches down the line.
By focusing on these areas, you’ll be better set to take advantage of all the benefits Type 5 construction has to offer. Smart planning and effective execution can make this a go-to choice for many of your commercial building needs.