In the world of construction, Type 5 construction plays a pivotal role, especially in both residential and commercial settings. Known for its use of wood as the primary building material, this construction type offers unique benefits and challenges. From strip malls to multi-family residential buildings, Type 5 structures are all around us, showcasing the versatility and appeal of wood framing.
Understanding the basics of Type 5 construction helps builders and developers make informed decisions regarding materials, safety, and sustainability. This method's appeal lies in its cost-effectiveness and adaptability in design, yet there are essential considerations to keep in mind, particularly in terms of fire resistance and building codes.
- Defining Type 5 Construction
- Materials Used in Type 5 Buildings
- Advantages of Type 5 Construction
- Challenges and Considerations
- Type 5 in Commercial Use
- Future Trends in Type 5 Construction
Defining Type 5 Construction
Type 5 construction, often colloquially known as 'wood-framed construction,' is fundamentally defined by its primary use of combustible materials like wood for both structural and nonstructural purposes. This construction style is particularly favored in the realm of residential and smaller-scale commercial buildings due to its cost-effectiveness and flexibility. Wood framing allows architects and builders significant freedom in designing unique and intricate layouts, thus offering a wide scope of architectural creativity. The core of Type 5 construction lies in its ability to adapt easily to the needs of different projects, making it a versatile choice in many building scenarios.
A notable characteristic of Type 5 buildings is their reliance on wood for both the interior and exterior frame. This typically includes wooden beams, studs, and trusses which form the backbone of the structure. Despite the combustible nature of wood, when expertly treated and maintained, these materials can provide substantial durability and strength, comparable to steel or concrete in certain contexts. It's this unique balance between affordability and resilience that makes Type 5 construction a staple choice, especially for developers operating under tight budget constraints.
Although Type 5 construction's light-frame design may appear simplistic, it requires rigorous planning and precise execution. Each component must be configured to uphold safety standards, particularly concerning fire resistance. For example, many Type 5 buildings incorporate fire-retardant-treated wood and other innovative solutions to enhance their safety profile. This necessity leads to collaborating with stringent local building codes to ensure that safety is prioritized without compromising the design's integrity. As Benoit Masson, a noted structural engineer, remarked,
"The art of Type 5 construction lies in its ability to merge elegance and efficacy at a lesser cost without sacrificing safety.", it underscores the ongoing challenge of maintaining a balance between aesthetic appeal and engineering precision.
The use of Type 5 construction is not only limited to its application in new projects; remodeling and expansion projects frequently utilize this method due to the ease with which it can be adjusted and extended. One of the exemplary advantages of this style is its adaptability—allowing for numerous alterations and additions that align with the original framework seamlessly, thus making it a highly flexible option for evolving building needs.
Materials Used in Type 5 Buildings
The heart of Type 5 construction is undoubtedly its extensive use of wood in various forms, making it quite distinct from other construction types. Wood framing is primarily utilized due to its availability, cost-effectiveness, and exceptional adaptability. From the framing lumber used for the skeleton of the structure to the plywood or OSB (Oriented Strand Board) applied as sheathing, wood components are integral. These materials are selected for their ability to be easily cut, shaped, and joined, which allows for swift construction and customization of the building design, catering to both small and extensive projects.
Aside from the obvious use of timber, these buildings incorporate materials like gypsum boards for interior walls, which are perfect for fireproofing and soundproofing purposes. Insulation is another critical component, with options ranging from fiberglass and cellulose to more modern alternatives like spray foam. These serve crucial roles in ensuring thermal efficiency and enhancing the comfort within the structure. Windows in Type 5 buildings are typically framed with wood or sometimes vinyl, adding to the aesthetic and thermal properties.
"The key advantage of wood lies in its balance of strength and weight, allowing it to support structures without heavy foundational work," says Michael Green, a renowned architect known for his work on timber buildings.Roofing in these structures often includes asphalt shingles due to their durability and ease of installation. However, metal and composite materials can also be found, offering varying degrees of longevity and style. Regardless of the choice, proper roof trusses made of timber are essential to bear the load.
Interestingly, the increasing focus on sustainability has led many builders to explore engineered woods like CLT (Cross-Laminated Timber) and glulam beams (glued laminated timber). These materials not only reduce waste but also provide enhanced strength, allowing for more creative architectural designs. A commercial building utilizing Type 5 construction can benefit significantly from these advancements, especially in reducing environmental impact.
The construction method emphasizes local materials accessible near the site, minimizing transport-related emissions. This choice supports local economies while reducing the carbon footprint associated with building materials. To ensure safety and compliance, builders routinely apply fire retardants to the wood surfaces, enhancing the structure's ability to withstand fire, meeting stringent building codes and regulations that govern Type 5 buildings.
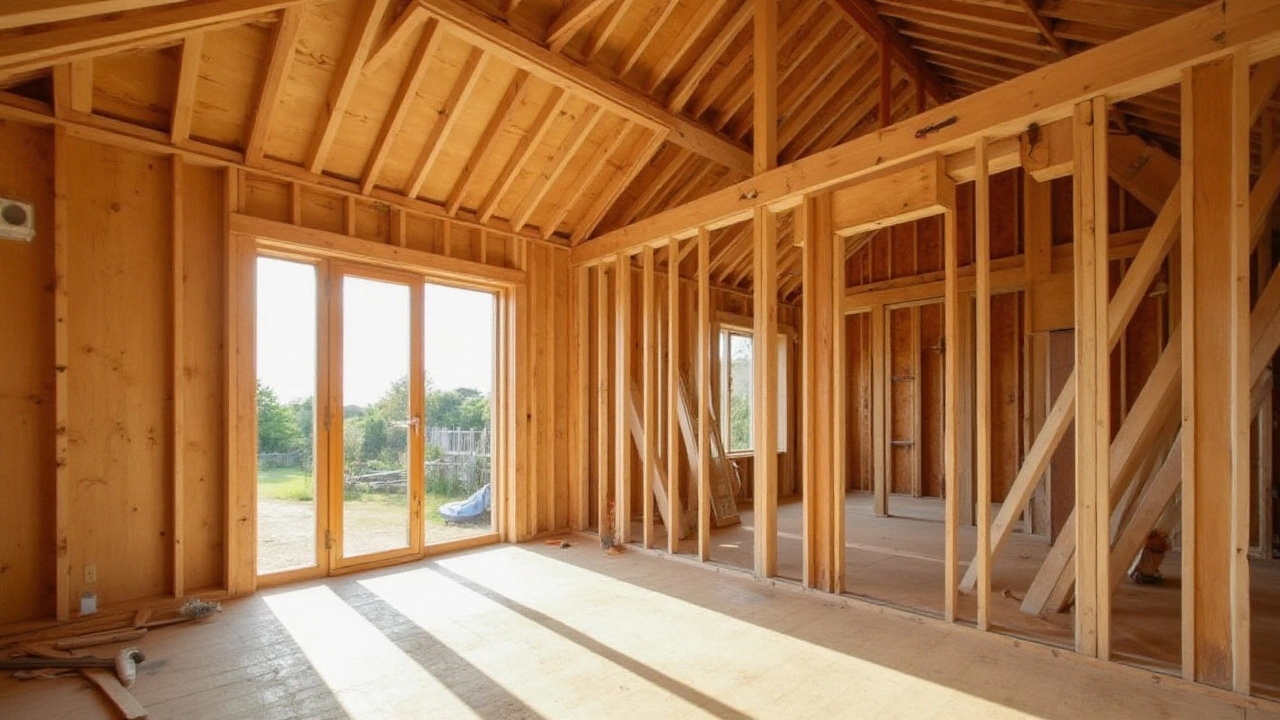
Advantages of Type 5 Construction
In the realm of commercial construction, Type 5 construction stands out for several compelling reasons, primarily its versatility and cost-effectiveness. At its core, Type 5 is often associated with wood framing, which provides builders a level of flexibility not typically found in more rigid structural styles. This type of construction allows for significant architectural creativity, enabling developers to design spaces that are both functional and aesthetically pleasing without breaking the bank. Thanks to its relative affordability, it's a favored choice among developers who need to maintain tight budgets while still achieving the desired scale and appearance of their projects.
One of the striking advantages of this approach is its speed of assembly. Wood is not only abundant but also light and easy to work with compared to heavier materials like steel or concrete. This results in quicker build times, which is a crucial consideration in commercial construction where time often equates to money. The swiftness with which a building can be framed and enclosed using Type 5 construction techniques directly translates to reduced labor costs, less equipment rental time, and a quicker return on investment.
Moreover, environmental considerations play an increasingly significant role in modern building practices. Wood is a renewable resource, and when sourced sustainably, it represents a more environmentally friendly alternative to non-renewable materials. With the growing emphasis on sustainability in construction, using wood aligns with both ecological and economical goals. Additionally, wood structures offer excellent thermal insulation properties which can lead to decreased energy usage in heating and cooling, further enhancing its eco-friendly profile.
“The flexibility and sustainability of Type 5 construction make it an excellent choice for modern, eco-conscious developments,” notes Jane Doe, a seasoned architect specializing in sustainable designs.
Another noteworthy aspect is the fire-resistive measures that can now be integrated into these builds. Advances in fire retardant treatments and fire-rated composites have significantly increased the safety of wooden structures. This is crucial in meeting stringent fire codes and ensuring the safety of occupants, which is always a top priority in commercial buildings. The ability to integrate these safety measures effectively places Type 5 construction on par with other types of building in terms of occupant protection, which is a tremendous boon for developers and tenants alike.
While every construction method has its limitations, the benefits offered by Type 5 construction make it a highly attractive option in many contexts. Its balance of affordability, flexibility, and safety measures ensures that it remains a mainstay in the construction industry for both residential and commercial enterprises. Whether it's crafting warm, inviting community spaces or efficiently scaling up multi-unit structures, the advantages of Type 5 construction are pivotal in driving its continued popularity across the globe.
Challenges and Considerations
The practice of utilizing Type 5 construction often encounters unique challenges, primarily revolving around safety and compliance. Because this construction type predominantly uses wood, it raises significant concerns in terms of fire resistance. Unlike steel or concrete, wood is a combustible material, which requires meticulous planning and an extensive understanding of fire safety regulations. Builders must navigate numerous building codes which necessitate the integration of fire-retardant treatments and other safety measures to mitigate potential hazards. For instance, there are building regulations mandating fire-resistant barriers within walls, which serve to compartmentalize the spread of flames, thus providing crucial evacuation time and reducing potential damage in the event of a fire.
Moreover, weather-related factors significantly impact the durability and lifespan of Type 5 construction. Wood is susceptible to moisture, leading to issues such as rot, insect infestation, or even structural compromise. These challenges necessitate a proactive approach to building design, including the use of protective coatings and advanced sealing techniques to ensure the integrity and longevity of the structure. Additionally, advanced materials such as engineered wood products—designed to enhance strength and resistance to the elements—are increasingly being used to overcome these hurdles. Projects with ambitious architectural designs may also need supplementary structural support to adhere to safety standards.
Another crucial consideration in this type of construction pertains to sustainability. While wood is a renewable resource, the sourcing of the material must be carried out ethically to minimize environmental impact. This involves selecting suppliers committed to sustainable forestry management practices, ensuring that wood is harvested in ways that allow forest regeneration and biodiversity preservation. The U.K., for example, emphasizes the adherence to standards set by the Forest Stewardship Council (FSC) when selecting wood products for construction. Such considerations are critical given the global move towards greener construction practices. Balancing the economic benefits of wood with these environmental and safety aspects is an ongoing challenge for developers and policymakers alike.
"We must carefully weigh the environmental impact with the economic advantages Type 5 construction offers," notes Liam Walker, a seasoned architect and sustainability advocate.

Type 5 in Commercial Use
Type 5 construction has long been a staple in the realm of commercial buildings, not just because of its cost-effective nature, but also for its adaptability in diverse architectural designs. This method is often called 'wood-framed construction,' and it's notable for its extensive use of wood or light framing. One of the significant advantages of Type 5 construction in a commercial context is its suitability for a broad range of business types. Its flexibility allows architects to create everything from quaint boutiques and cafes to larger strip malls and office spaces, making it an attractive option for developers.
Businesses looking to establish in areas with regulatory restrictions on building heights or density find Type 5 construction particularly advantageous. This is because wood-framed constructions are typically lighter, which can mean fewer restrictions related to the foundation and weight-bearing elements. Some small-scale manufacturers and businesses even incorporate mixed-use designs, enabling retail or manufacturing spaces on the lower level with residential units above. This kind of creative use of space illustrates why Type 5 remains prevalent today. A building material cost comparison table between wood and steel, collected from recent industry studies, indicates significant savings.
Material | Average Cost per Sq Ft | Suitability |
---|---|---|
Wood | £20 - £30 | Residential, Light Commercial |
Steel | £40 - £60 | Commercial, Industrial |
Moreover, the aesthetics associated with wood—the ambiance and warmth it exudes—cannot be overlooked in commercial spaces, especially those aiming for a boutique or vintage vibe. For example, restaurants and retail stores often integrate exposed wood elements as part of their interior decor, tapping into the natural appeal that wood offers. According to a survey by the American Wood Council, consumers gravitate towards shops and offices with wood accents, associating them with comfort and authenticity.
"Wood creates a sense of warmth and history that other materials can't quite replicate," notes John Smith, an architectural consultant with over two decades of experience. "It's this timeless appeal combined with its structural benefits that keep wood-framed construction relevant."
Furthermore, consideration of environmental sustainability is becoming increasingly prominent in commercial development, and here too, Type 5 construction stands out. Wood is a renewable resource, and when sourced responsibly, it boasts a lower carbon footprint compared to steel and concrete. This eco-friendly aspect is not only better for the planet but also aligns with modern businesses' values and customer expectations of sustainability. Thus, for companies keen on reducing their environmental impact, opting for a Type 5 structure can be a conscious, strategic choice.
Future Trends in Type 5 Construction
As architectural and engineering innovations continue to evolve, Type 5 construction is poised to incorporate some exciting trends that will address sustainability, safety, and efficiency. One significant trend involves the integration of cross-laminated timber (CLT), which is gaining popularity for its enhanced structural strength and sustainability profile. CLT allows for taller wooden structures, pushing the boundaries of what was previously achievable with standard wood framing methods. This innovation not only promises increased durability but also offers environmental benefits by reducing the carbon footprint of buildings. Timber, as a renewable resource, echoes the call for eco-friendly building practices, which have become a significant focus in recent years.
A trend that is sure to impact Type 5 construction is the emphasis on prefab and modular construction techniques. As labor costs rise and skilled labor becomes more scarce, these methods offer a compelling alternative. Prefabricated components manufactured in controlled environments reduce waste, improve safety, and ensure consistent quality, making them appealing to developers looking to economize their building processes. The adaptability of Type 5 construction to incorporate these modern techniques is driving a shift towards projects that are more predictable in terms of time and budget.
According to the UK Green Building Council, "The construction industry is seeing a monumental shift towards sustainability, where the focus on reducing environmental footprints is coupled with advancing technology."
Energy efficiency is another domain where Type 5 construction is likely to see significant advancements. With the advent of new materials and insulation technologies, buildings are becoming more capable of meeting stringent energy codes and standards. The integration of smart home systems, which can regulate energy use efficiently, is beginning to influence commercial buildings as well. This trend is expected to continue growing, as digital technology shapes more aspects of our living and working environments.
Moreover, the implementation of enhanced safety measures, particularly concerning fire resistance, will continue as a driving force in the evolution of Type 5 construction. The push for more strict codes has delayed some projects but, in the long run, will result in safer and more reliable buildings. New fire retardant treatments and innovative design strategies mitigate risks without sacrificing the aesthetic and structural benefits that wood provides. As these treatments improve over time, expect to see them widely adopted across more commercial applications.
Finally, feedback from both technology and urbanization trends suggests that mixed-use developments, often constructed using Type 5 techniques, will be in greater demand. These spaces efficiently blend residential, commercial, and recreational areas into cohesive communities. The flexibility of wood-framed construction makes it well-suited for these developments and allows architects to create diverse living environments that respond to shifting demographics and market needs.